Have you ever found yourself in a power outage, only to realize your Honeywell generator won’t start? It’s a frustrating situation that can leave you feeling helpless, especially when you need it the most. You’re not alone—many people face this issue at some point.
In this article, you’ll discover common reasons why your generator might be refusing to cooperate and simple troubleshooting tips to get it running again. Whether it’s a fuel problem, a battery issue, or something else, you’ll find practical solutions that can save you time and stress. Let’s get your generator back to work so you can enjoy peace of mind during those unexpected outages.
Key Takeaways
- Common Issues: Honeywell generators may fail to start due to fuel supply problems, battery and electrical issues, or blockages in the air filter and carburetor.
- Troubleshooting Steps: Check fuel levels, inspect the battery for charge and corrosion, and examine all electrical connections to identify potential issues.
- Professional Help: Seek professional assistance if the generator persists in not starting, produces unusual noises, emits strong odors, or shows signs of smoke or sparks.
- Routine Maintenance: Regularly inspect and maintain your generator’s fuel system, battery, electrical connections, and air filter to prevent starting issues.
- Seasonal Checks: Prepare your generator for seasonal changes by performing pre-winter and pre-summer maintenance to ensure optimal performance year-round.
Common Causes of Honeywell Generator Issues
When your Honeywell generator won’t start, several common issues could be causing the problem. Understanding these can help you troubleshoot effectively.
Fuel Supply Problems
Issues with the fuel supply often prevent the generator from starting. Ensure that there’s enough fuel in the tank. Check for contaminants in the fuel, as dirty fuel can clog the system. Inspect the fuel lines for leaks or blockages, as these can disrupt the flow of fuel to the engine. Regularly replacing the fuel filter can also help maintain optimal performance.
Battery and Electrical Issues
Battery-related issues frequently lead to starting problems. Verify that the battery is fully charged. Corroded terminals can hinder electrical flow, so clean them if necessary. Check the connections for any looseness. If the battery shows signs of age, like swelling or leaks, consider replacing it. Additionally, test the fuses and circuit breakers for any tripped switches or blown fuses.
Air Filter and Carburetor Blockages
Blocked air filters and carburetor malfunctions can restrict airflow, causing starting difficulties. Inspect the air filter and replace it if it appears dirty or clogged. Ensure the carburetor isn’t gummed up with fuel residues. If cleaning the carburetor doesn’t resolve the issue, you might need to rebuild or replace it. Routine maintenance helps keep airflow clear and can prevent these issues from arising.
Troubleshooting Steps for Honeywell Generators
Follow these key troubleshooting steps to identify and fix issues preventing your Honeywell generator from starting.
Checking Fuel Levels
Verify the fuel tank. Ensure it’s filled with fresh fuel, as old or contaminated fuel can cause starting problems. Look for any signs of sediment or water in the tank, as those contaminants negatively impact performance. If the fuel level seems low, refill it, and if you suspect contamination, drain and replace the fuel for optimal results.
Inspecting the Battery
Examine the battery condition. Ensure the battery charge is sufficient, as a weak battery often leads to starting failures. Use a multimeter to check the voltage; it should read between 12.4 and 12.7 volts when fully charged. Look for corroded terminals or loose connections, as these can hinder performance. Clean any corrosion and tighten connections as needed to restore proper function.
Examining Electrical Connections
Inspect all electrical connections. Check the wiring for any signs of damage, wear, or corrosion. Ensure that connections are securely fastened. A loose or damaged connection can disrupt the power flow and prevent the generator from starting. Wiggle the wires gently to ensure they’re not loose and replace any frayed or damaged wires immediately to maintain reliability.
When to Seek Professional Help
If troubleshooting didn’t resolve your Honeywell generator issue, knowing when to seek professional help becomes crucial. Certain problems require the expertise of a qualified technician.
Signs Your Generator Needs Repair
- Persistent No-Start: If your generator still won’t start after completing basic checks, it’s time to consult a professional.
- Unusual Noises: Sounds like grinding, knocking, or excessive rattling indicate internal problems.
- Strong Odors: Smells of fuel or burning could signal leaks or electrical malfunctions.
- Frequent Shutdowns: If your generator shuts down unexpectedly, structural or mechanical issues may exist.
- Smoke or Sparks: Any signs of smoke or sparking connectors warrant immediate professional attention.
- Research Certified Technicians: Look for technicians with certification specific to Honeywell generators. Their knowledge ensures proper repairs.
- Read Reviews: Check online reviews and ratings. Feedback from previous customers highlights a technician’s reliability and quality of service.
- Ask for Recommendations: Seek referrals from friends or family who’ve used generator repair services. Personal experiences often guide you to skilled professionals.
- Get Multiple Quotes: Contact several technicians to compare prices. This approach helps you find fair rates while ensuring quality repairs.
- Verify Licenses and Insurance: Always confirm that the technician holds the necessary licenses. Insurance protects you against potential liabilities.
Maintenance Tips to Prevent Starting Issues
Perform regular maintenance to keep your Honeywell generator in good working order. Consistent care can prevent starting issues and ensure reliable power during outages.
Regular Inspections
Conduct routine inspections to identify potential problems before they escalate. Check the following components:
- Fuel System: Look for leaks in fuel lines and inspect the fuel filter. Replace filters every 100 hours of use or annually, whichever comes first.
- Battery: Test the battery voltage regularly. Maintain a charge of at least 12.6 volts. Clean terminals free of corrosion, using a mixture of baking soda and water when necessary.
- Electrical Connections: Inspect all wiring and connectors for fraying or damage. Tighten loose connections to ensure reliable electrical flow.
- Air Filter: Examine the air filter for dirt and obstruction. Clean or replace it every 6 months or after 100 hours of operation.
Seasonal Preparation
Prepare your generator for seasonal changes to maintain its performance. Take these steps each season:
- Pre-Winter Checks: Ensure the fuel tank is full, using fresh fuel mixed with stabilizer to prevent degradation. Start the generator to run for at least 30 minutes, confirming its operation.
- Pre-Summer Maintenance: Inspect the cooling system and ensure the generator can operate in high temperatures. Clean debris from around the unit and check the battery charge to avoid overheating.
- Storage Considerations: When storing, cover the generator to protect it from moisture and dust. Keep it in a dry area, and disconnect the battery if not using for an extended period.
Adhering to these maintenance tips helps avoid starting issues and prolongs the life of your Honeywell generator.
Conclusion
Dealing with a Honeywell generator that won’t start can be frustrating but you’re not alone. By following the troubleshooting tips and maintenance practices outlined in this article you can tackle common issues and get your generator back up and running.
Always remember to keep an eye on fuel levels battery condition and air filters to ensure smooth operation. If the problem persists don’t hesitate to reach out to a professional. With a little care and attention your generator will be ready to power your home when you need it most. Stay prepared and keep the lights on!
Frequently Asked Questions
Why won’t my Honeywell generator start during a power outage?
Generator failures can stem from various issues, including inadequate fuel supply, battery troubles, or blockages in the air filter or carburetor. Check your fuel levels, battery charge, and ensure airflow is not obstructed to identify the cause.
How can I troubleshoot my Honeywell generator?
Start by verifying the fuel level and ensuring it’s fresh and clean. Then, inspect the battery for proper charge and connections. Finally, look for any damaged electrical connections and replace or repair them as needed.
When should I seek professional help for my generator?
Consider calling a technician if your generator won’t start despite troubleshooting, emits unusual noises, has strong odors, frequently shuts down, or shows signs of smoke or sparks. These may indicate deeper issues requiring expert attention.
What regular maintenance should I perform on my Honeywell generator?
Regular maintenance includes checking the fuel system for leaks, testing battery voltage, inspecting and cleaning electrical connections, and replacing air filters as needed. Consistent upkeep can prevent starting issues and ensure reliable performance.
How do I find a qualified technician for my generator?
Search for certified professionals by reading reviews online, asking for recommendations from friends, and gathering multiple quotes. Always verify licenses and insurance to ensure you hire a qualified technician for your Honeywell generator needs.
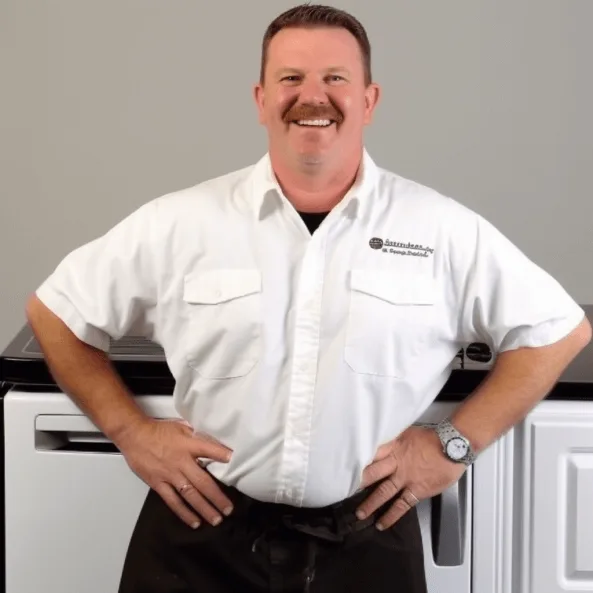
Hey, I’m Jake. I focus on cooling systems at Appliance Mastery, like fridges, freezers, and air conditioners.
I’ve worked in appliance repair for more than ten years and I’m certified through NASTeC. I’ve seen just about every fridge issue you can imagine.
My goal is to help you fix problems without stress. Whether it’s a freezer that won’t cool or an AC that keeps beeping, I’m here to walk you through it.