Have you ever reached for a refreshing drink only to find your Sub Zero freezer drawer ice maker isn’t working? You’re not alone. Many people face this frustrating issue, especially during hot summer days when ice is a must.
In this article, you’ll discover common reasons your ice maker might be on the fritz and how to troubleshoot the problem. With a few simple steps, you can get back to enjoying ice-cold beverages in no time. Whether you’re a seasoned DIYer or just looking for some guidance, you’ll find helpful tips to restore your ice maker’s functionality.
Key Takeaways
- Common Issues Identified: Ice makers often face problems such as no ice production, slow ice production, and ice clumping due to factors like water supply blockages or temperature settings.
- Key Components: Understanding the main components, including the ice mold, water supply line, and thermostat, is crucial for effective troubleshooting.
- Troubleshooting Steps: Regularly inspect the water line, ice mold, and thermostat, and check the power supply to resolve common issues impacting ice production.
- Importance of Maintenance: Perform regular cleaning and maintenance, including checking the water filter and temperature settings, to prevent buildup and ensure optimal performance.
- When to Seek Help: If problems persist after troubleshooting, consider scheduling service with a professional to diagnose potential mechanical and electrical failures.
- Temperature Settings Matter: Keeping your freezer’s temperature between 0°F and 5°F is vital for efficient ice production.
Overview of Sub Zero Freezer Drawer Ice Makers
Sub Zero freezer drawer ice makers are designed for convenience, providing easy access to ice for your drinks. Regular maintenance keeps them running efficiently, especially during warmer months.
Components of the Ice Maker
- Ice Mold: This part shapes the water into ice cubes. It can become clogged or frozen if not cleaned regularly.
- Water Supply Line: This delivers water from your home plumbing to the ice maker. A kinked or blocked line can result in no ice production.
- Thermostat: This regulates the temperature inside the ice maker. If it fails, it can affect ice production and quality.
Common Issues
- No Ice Production: This might stem from improper water supply or electrical issues. Check the water line for blockages and ensure the appliance is plugged in.
- Slow Ice Production: This can occur if the temperature is set too high. Lowering the freezer’s temperature usually speeds up the process.
- Ice Clumps: Clumped ice indicates moisture problems or temperature fluctuations. Ensure proper sealing of the freezer drawer to minimize humidity.
Troubleshooting Tips
- Inspect the Water Line: Look for kinks or obstructions. Clear any blockages and check the connection to the plumbing.
- Check the Ice Mold: Remove any ice build-up. Clean the mold with warm water to ensure it generates ice efficiently.
- Adjust the Temperature: Set the freezer to a temperature of 0°F. This generally helps improve ice production.
- Examine the Drain: Ensure the drain is clear. A blocked drain can cause water to back up and affect ice production.
- Regular Cleaning: Clean the ice maker every few months. This prevents build-up and keeps it functioning well.
- Monitor Usage: Keep an eye on how often the ice maker runs. If it’s not producing enough ice, review the troubleshooting tips above.
- Schedule Service: If problems persist, consider contacting a professional to evaluate your appliance.
By ensuring these elements function correctly, you maintain optimal performance.
Common Issues with Ice Makers
Ice makers can experience various issues that affect their performance. Here’s a look at common problems and their potential solutions.
Mechanical Failures
Mechanical failures in your ice maker often stem from worn or damaged components.
- Ice Mold Issues: Check for cracks or damage in the ice mold, which can prevent proper ice formation.
- Obstructed Moving Parts: Inspect the arm or paddle for blockages. Food debris can impede movement, leading to ice production issues.
- Water Supply Blockage: Ensure the water supply line isn’t kinked or blocked. A restricted water flow can stop ice production altogether.
Electrical Problems
Electrical problems can disrupt your ice maker’s operation.
- Thermostat Malfunction: Verify that the thermostat is functioning correctly. A faulty thermostat can lead to incorrect temperatures, affecting ice production.
- Power Supply Issues: Ensure your ice maker is plugged in and receiving power. Check for blown fuses or tripped circuit breakers that may cut off electricity.
- Control Board Failures: If other solutions don’t work, the control board might be faulty. Inspect for signs of damage or burnt connections, and consider contacting a professional for replacement.
By addressing these mechanical and electrical issues promptly, you can restore your Sub Zero freezer’s ice maker functionality and keep your drinks refreshingly cold.
Troubleshooting the Ice Maker
If your Sub Zero freezer drawer ice maker isn’t working, several factors could be causing the issue. Follow these steps for effective troubleshooting.
Checking Power Supply
- Confirm Power Connection: Ensure the freezer is plugged in and the outlet is functional. Test the outlet with another device if needed.
- Inspect Reset Switch: Look for the ice maker’s reset switch, often located inside or on the control panel. Press it if you find one.
- Examine Circuit Breaker: Check the circuit breaker for tripped switches. Reset any tripped breakers to restore power.
Examining Water Supply
- Inspect Water Line: Check the water supply line for kinks or blockages that could hinder water flow. A clear line is essential for ice production.
- Verify Water Supply: Ensure the water valve is fully open. This valve controls water flow to the ice maker.
- Assess Water Filter: Consider replacing the water filter if it’s clogged. A new filter can improve water flow and quality.
- Examine Ice Mold: Check the ice mold for ice build-up or obstruction. Clear any ice or debris from the mold as needed.
- Check the Thermostat: Ensure the thermostat is set to a cold enough temperature. Adjust it if necessary and monitor the ice production.
- Inspect Moving Parts: Look for any wear on the moving components of the ice maker. Lubricate if applicable or consider replacing worn parts.
By following these troubleshooting steps, you can identify and address the issues affecting your Sub Zero freezer drawer ice maker’s performance.
Maintenance Tips for Optimal Performance
Maintaining your Sub Zero freezer drawer ice maker ensures efficient operation and prevents issues. Following practical advice helps keep your ice maker performing at its best.
Regular Cleaning Practices
Keep the ice maker clean to prevent ice build-up and clogs. Clean the ice mold every three months, removing any dirt or debris.
- Unplug the unit to ensure safety during cleaning.
- Remove the ice bin and clean it with warm soapy water. Rinse thoroughly before replacing.
- Wipe the exterior with a microfiber cloth to eliminate dust and grime.
- Inspect the water filter to ensure it’s not clogged. Replace it every six months or according to the manufacturer’s recommendations.
- Check the drain for blockages. Clear any debris that may hinder water flow.
Temperature Settings
Correct temperature settings play a crucial role in ice production. Set your freezer drawer between 0°F and 5°F for optimal ice making.
- Use a thermometer to verify the internal temperature.
- Adjust the thermostat if necessary. If it reads higher than recommended, consider lowering it incrementally until ice production improves.
- Avoid overloading the freezer. Overcrowding can restrict airflow, affecting temperature consistency.
Taking these steps helps maintain the performance of your Sub Zero freezer drawer ice maker, ensuring a steady supply of ice for your needs.
Conclusion
Getting your Sub Zero freezer drawer ice maker back in action doesn’t have to be overwhelming. With a bit of troubleshooting and regular maintenance, you can tackle most issues that arise. Remember to check the basics like the water supply and temperature settings before diving deeper into repairs.
If you find yourself stuck after trying the tips mentioned, don’t hesitate to reach out for professional help. Keeping your ice maker in top shape ensures you’ll always have ice on hand for those hot days and refreshing drinks. Enjoy the convenience of your Sub Zero freezer and stay cool all summer long!
Frequently Asked Questions
What causes ice makers in Sub Zero freezers to stop working?
Ice makers can stop working due to issues like a blocked water line, malfunctioning thermostat, dirty ice mold, or power supply problems. Regular maintenance and inspection of these components can help identify the cause.
How can I troubleshoot my Sub Zero ice maker?
Start by checking the power supply, inspecting the water line for kinks, and ensuring the water valve is open. Next, assess the ice mold for obstructions and verify that the thermostat settings are correct.
How often should I clean my Sub Zero ice maker?
It’s recommended to clean your ice maker every three months. Regular cleaning helps maintain optimal performance and prevents clogs or buildup that can hinder ice production.
What temperature should my Sub Zero freezer be set at for optimal ice production?
To ensure efficient ice production, set your Sub Zero freezer drawer temperature between 0°F and 5°F. This range helps maintain adequate conditions for ice formation.
When should I consider professional service for my ice maker?
If troubleshooting steps do not resolve the issue with your ice maker, or if you notice mechanical or electrical failures, it’s best to schedule professional service to prevent further damage.
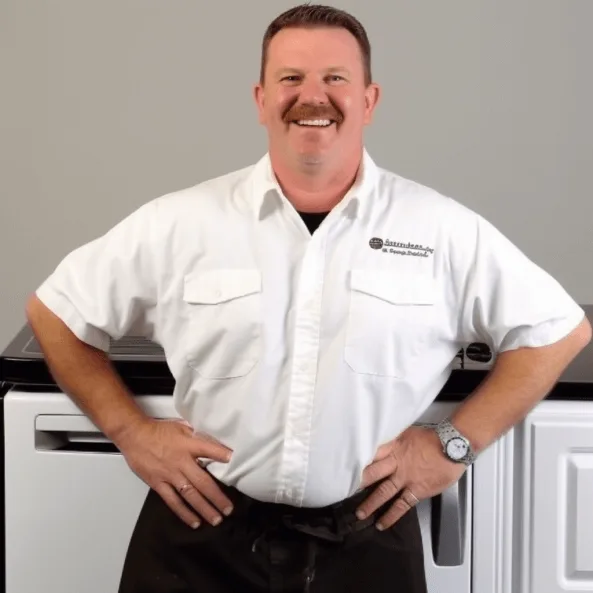
Hey, I’m Jake. I focus on cooling systems at Appliance Mastery, like fridges, freezers, and air conditioners.
I’ve worked in appliance repair for more than ten years and I’m certified through NASTeC. I’ve seen just about every fridge issue you can imagine.
My goal is to help you fix problems without stress. Whether it’s a freezer that won’t cool or an AC that keeps beeping, I’m here to walk you through it.