Is your Carrier heat pump compressor refusing to start? You’re not alone. Many homeowners face this frustrating issue, especially during extreme weather when you need your system the most.
Understanding why your compressor isn’t running can save you time and money. This article will guide you through common causes and simple troubleshooting steps. You’ll learn how to identify potential problems and when it’s best to call a professional. With the right knowledge, you can get your heat pump back on track and keep your home comfortable.
Key Takeaways
- Identify Common Issues: Power supply problems, thermostat malfunctions, and electrical component failures are the most frequent causes of a Carrier heat pump compressor not running.
- Power Supply Checks: Ensure circuit breakers are not tripped, fuses are intact, and that all wiring connections are secure to restore power to the heat pump.
- Thermostat Functionality: Confirm the thermostat is set correctly, check for low batteries, and consider testing with an alternative thermostat if issues persist.
- Perform Regular Maintenance: Schedule annual professional servicing, clean the unit regularly, and monitor refrigerant levels to maintain efficiency and extend the lifespan of your heat pump.
- Recognize When to Seek Help: Unusual noises, frequent cycling, poor temperature regulation, visible damage, or foul odors are signs that it’s time to consult an HVAC professional.
- Choose the Right Technician: Verify credentials, read reviews, compare estimates, and inquire about warranties to ensure you select a qualified HVAC technician for repairs.
Common Causes of Carrier Heat Pump Compressor Not Running
Understanding why your Carrier heat pump compressor isn’t running can help you address the issue quickly. Several common causes can prevent the compressor from operating effectively.





Power Supply Issues
Power supply problems often stand as the primary reason your heat pump compressor won’t start. Check these key points:
- Tripped Circuit Breaker: A tripped breaker can cut off power. Check your electrical panel and reset any tripped breakers.
- Blown Fuse: Inspect for blown fuses and replace them if necessary. This can restore power to the unit.
- Disconnected Wiring: Loose or disconnected wires may interrupt the power supply. Examine all accessible wiring to ensure secure connections.
Thermostat Problems
Your thermostat controls the heat pump’s operations. If there’s a malfunction, the compressor may not run. Consider these scenarios:
- Incorrect Settings: Ensure the thermostat is set to heat mode and that the desired temperature is higher than the current room temperature.
- Battery Issues: If your thermostat uses batteries, replace them if they’re low or dead. This might revive functionality.
- Faulty Thermostat: A malfunctioning thermostat can prevent proper signals from reaching the compressor. Test it by switching to a different setting and see if there’s any response.
Electrical Component Failures
Electrical component failures can also cause the compressor to stop running. Investigate these elements:
- Capacitor Issues: The capacitor provides the initial boost for starting the compressor. Signs of a faulty capacitor include clicking sounds or an inability to start.
- Compressor Relay Failure: A bad relay can hinder the compressor’s operation. If your heat pump seems to engage but fails to start completely, check the relay for defects.
- Control Board Problems: The control board directs power to various components. A malfunction here might prevent your compressor from receiving power altogether.
By reviewing these common causes and examining your system accordingly, you can troubleshoot effectively or determine if it’s time to call a professional for further assistance.
Troubleshooting Steps
Troubleshooting a Carrier heat pump compressor not running involves a few systematic steps. Following these guidelines can help identify the problem and ensure your system operates efficiently.





Checking the Power Supply
- Inspect Circuit Breakers: Verify that the circuit breakers haven’t tripped. A tripped breaker needs resetting.
- Examine Fuses: Check for blown fuses, as they can disrupt power flow. Replace any faulty fuses.
- Confirm Power Connection: Ensure the heat pump is plugged in, and no wiring is loose or damaged. Tighten any connections if needed.
Inspecting the Thermostat
- Set Correct Temperature: Ensure the thermostat is set to heat mode and the temperature is higher than the current indoor temperature.
- Check Batteries: If your thermostat requires batteries, replace them if they are dead.
- Assess Functionality: If the thermostat lights up but still doesn’t respond, it may be faulty. Consider testing with a different thermostat to see if the problem persists.
- Inspect Wiring: Examine all visible wiring for signs of wear, fraying, or disconnection. Repair any damaged wires.
- Check Capacitor and Relay: Look for a bulging capacitor or signs of corrosion on the compressor relay. Indications of failure require replacement.
- Examine Control Board: Inspect the control board for burned components or loose connections. A malfunctioning board can prevent the compressor from running.
By taking these troubleshooting steps, you can effectively diagnose issues with your Carrier heat pump compressor. If problems persist beyond these checks, professional assistance may pose the best solution.
Maintenance Tips for Carrier Heat Pumps
Regular maintenance keeps your Carrier heat pump running efficiently and extends its lifespan. Implement these maintenance tips to ensure optimal performance.
Regular Servicing
Schedule professional servicing at least once a year. Technicians can inspect components, identify potential problems, and perform necessary repairs. During servicing, the technician checks for refrigerant leaks, cleans coils, and assesses electrical connections. Keeping records of servicing can help track maintenance histories and anticipate future needs.
Cleaning the Unit
Keep the heat pump clean by regularly removing dirt and debris. Start by turning off the power to the unit. Use a garden hose to gently wash the outdoor coils, ensuring water doesn’t enter electrical components. Check and clean the air filter every month. Replace it if it’s dirty; a clean filter improves airflow and system efficiency.
Checking Refrigerant Levels
Monitor refrigerant levels to ensure your heat pump operates correctly. Low refrigerant can cause the compressor to overheat and stop running. If you suspect low refrigerant, check for ice build-up on the coils or a drop in cooling efficiency. Contact a professional to handle refrigerant issues. They’ll measure levels and recharge the system as necessary.





Implement these tips consistently to maintain your Carrier heat pump’s functionality. Regular attention to servicing, cleaning, and refrigerant levels can prevent larger issues and keep your heat pump operating effectively when you need it most.
When to Call a Professional
Recognizing when to call a professional can save time and prevent further damage to your Carrier heat pump. If simple troubleshooting doesn’t resolve the issue, seeking expert help becomes essential.
Signs of Serious Issues
Knowing the signs of serious issues helps you decide when to call a technician. Look for these indicators:
- Unusual Noises: Loud clanking or grinding sounds can signal mechanical problems.
- Frequent Cycling: If your compressor turns on and off constantly, it may indicate a refrigerant leak or electrical issue.
- Poor Heating or Cooling: Noticeable drops in temperature output despite adjustments often reflect compressor or airflow issues.
- Visible Damage: Burn marks, fluid leaks, or damaged components on the unit require immediate attention.
- Foul Odors: Strange smells may indicate burnt wires or electrical problems.
If you notice any of these signs, professional assessment and repair are necessary to avoid safety risks or costly fixes.
Choosing the Right HVAC Technician
Selecting a qualified HVAC technician ensures effective repairs and peace of mind. Here are tips to help with that decision:
- Check Credentials: Ensure the technician is licensed and insured to work in your area. This protection covers liability and guarantees quality work.
- Read Reviews: Look for customer feedback online. Positive testimonials indicate good service and reliability.
- Ask for Estimates: Request quotes from multiple technicians to compare pricing. Be wary of unusually low bids as they can suggest subpar work.
- Verify Experience: Choose a technician who specializes in or has experience with Carrier systems. Specialized knowledge streamlines repairs.
- Inquire About Warranties: A reliable technician should offer warranties on work completed. This guarantees satisfaction and accountability.
By keeping an eye out for warning signs and knowing how to choose the right technician, you can ensure your heat pump gets the expert attention it needs promptly.
Conclusion
Dealing with a Carrier heat pump compressor that won’t run can be frustrating especially when you need it most. By understanding the potential causes and following the troubleshooting steps outlined in the article you can often resolve the issue yourself. Remember to keep an eye on maintenance to prevent future problems and ensure your system runs smoothly.
If you notice persistent issues or signs of serious trouble it’s always best to call in a professional. They can provide the expertise needed to get your heat pump back on track. Staying proactive about your heat pump’s health will help you maintain a comfortable home year-round.
Frequently Asked Questions
Why won’t my Carrier heat pump compressor start?
Your Carrier heat pump compressor might not start due to power supply issues, such as tripped circuit breakers, blown fuses, or disconnected wiring. It’s essential to check the thermostat settings and ensure it’s functioning properly as well. If the problem persists after basic checks, further diagnosis may be needed.
How can I troubleshoot my heat pump compressor?
Start by checking your circuit breakers and fuses for any issues. Next, verify the thermostat settings and replace the batteries if needed. Inspect the wiring for damages and examine the capacitor and compressor relay. If you see signs of failure, consult a professional.
When should I call a professional for my heat pump?
Call a professional if you notice unusual noises, frequent cycling, poor heating or cooling, visible damage, or bad odors coming from your heat pump. These signs could indicate serious issues that require expert assessment.
What maintenance steps can I take to ensure my heat pump runs efficiently?
To keep your heat pump running efficiently, schedule professional servicing at least once a year for inspections and repairs. Regularly clean the unit, check and change the air filter, and monitor refrigerant levels. Keeping up with maintenance prevents larger issues down the line.
How do I choose the right HVAC technician?
When selecting an HVAC technician, check their credentials, read customer reviews, and ask for estimates. Make sure to verify their experience and inquire about warranties. A qualified technician will ensure your heat pump receives the necessary care and repairs.
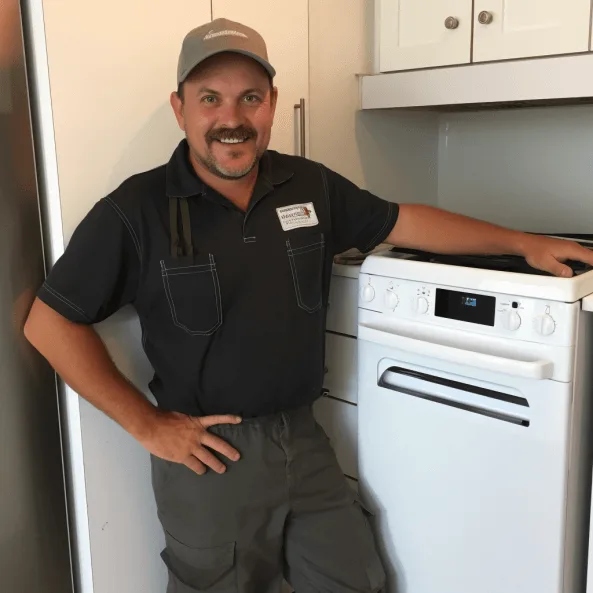
Hi, I’m Charlie, and I cover all things laundry here at Appliance Mastery.
I’ve spent over eight years working on washing machines, dryers, and dishwashers. I also have a degree in mechanical engineering, which helps me understand how these appliances really work.
I try to make every guide clear and practical. If you’re stuck with a noisy dryer or a leaking washer, I’ll help you figure out what’s wrong and how to fix it.