Have you ever opened your deep freezer to find everything thawed and a little too warm? It’s frustrating when your compressor stops working, leaving you worried about your food and money. You’re not alone; many people face this problem, and it can feel overwhelming.
Key Takeaways
- Identify Common Symptoms: Unusual noises and temperature fluctuations in your deep freezer often signal compressor issues that need immediate attention.
- Know the Causes: Electrical problems, mechanical failures, and blocked condenser coils are common causes of a failing compressor that can be diagnosed with proper troubleshooting.
- Follow Troubleshooting Steps: Begin by verifying the power supply, inspecting the thermostat, and cleaning the condenser coils to address compressor malfunctions effectively.
- Recognize When to Call a Professional: Signs like consistent loud noises, drastic temperature changes, or burning smells indicate it’s time to seek expert repair services.
- Choose the Right Technician: Ensure the technician is licensed, read customer reviews, request estimates, and inquire about their experience and warranty offerings for peace of mind in repairs.
Common Signs Of A Deep Freezer Compressor Not Working
Recognizing the signs of a failing compressor can help you tackle issues before they worsen. Here are some common symptoms to look for.
Unusual Noises
Listen for odd sounds coming from your deep freezer. A malfunctioning compressor may produce loud humming, clicking, or buzzing noises. If it sounds louder than usual, this often indicates a problem within the compressor or its components. Occasionally, you might hear a continuous running sound, which suggests it’s struggling to maintain temperature.





Temperature Fluctuations
Monitor the temperature inside your deep freezer. If items frequently thaw and refreeze, the compressor might not be functioning properly. A stable environment typically keeps food at 0°F (-18°C) or lower. If the temperature drifts above that mark, check for signs of compressor failure. You might notice frost buildup in odd places or inconsistent cooling throughout the unit. These fluctuations can lead to food spoilage, which makes identifying this issue critical.
Possible Causes Of Compressor Failure
Compressor failure often stems from several key issues. Identifying these causes can help resolve the problem quickly.
Electrical Issues
Electrical issues commonly affect compressor performance. Loose or damaged wiring might disrupt power flow. Check connections for wear or disconnection. Tripped circuit breakers can also halt function. Reset breakers and inspect fuses for damage. An inconsistent power supply can cause voltage fluctuations, leading to compressor strain. Use a multimeter to monitor voltage levels and ensure they stay within the manufacturer’s specifications.
Mechanical Failures
Mechanical failures frequently lead to compressor breakdown. Over time, wear and tear can impact components like the motor, bearings, or valves. Listen for unusual noises that indicate internal damage. A lack of lubrication can also cause excessive friction, which harms the compressor’s efficiency. Regular maintenance, such as lubrication checks, can prevent these issues. If you notice overheating, it may signal mechanical failure. Evaluate the compressor’s temperature against recommended operating ranges.
Blocked Condenser Coils
Blocked condenser coils significantly impair compressor functionality. Dust and debris accumulation can obstruct airflow. Regular cleaning of the coils helps maintain efficiency. Inspect the coils for blockages and clear them as necessary. Adequate airflow keeps the compressor functioning properly and reduces the risk of overheating. Additionally, check for any signs of ice buildup, which can occur when coils are covered or dirty. Maintaining clean coils can prolong compressor life and enhance overall performance.





Troubleshooting Steps
Troubleshooting a malfunctioning deep freezer compressor involves checking several key components. Follow these steps to diagnose and potentially resolve the issue.
Check Power Supply
- Confirm Power Source: Ensure the freezer is plugged in securely. Inspect the outlet for power by plugging in another device.
- Examine Circuit Breaker: Check your circuit breaker for any tripped switches. If the breaker is off, flip it back on and see if the compressor restarts.
- Inspect Power Cord: Look for any visible damage to the power cord. Replace it if frayed or broken to ensure proper functionality.
Inspect the Thermostat
- Adjust Temperature Setting: Verify the thermostat settings. If set too low, increase it and wait for the compressor to kick in.
- Check for Proper Placement: Ensure the thermostat is not covered or obstructed, as this can give inaccurate readings and prevent the compressor from working.
- Test the Thermostat: Consider using a multimeter to check the thermostat’s continuity. Replace it if it fails to show continuity when set to on.
- Locate the Coils: Find the condenser coils, typically at the back or beneath the unit. Accessibility may vary by model.
- Remove Dust and Debris: Use a vacuum or brush to clear away dust and dirt. Blocked coils can hinder cooling efficiency and affect the compressor.
- Schedule Regular Cleaning: Establish a routine for cleaning the coils every six months to maintain the freezer’s performance.
When To Call A Professional
Recognizing when to seek professional assistance is crucial for a malfunctioning deep freezer compressor. If troubleshooting doesn’t resolve the issue, it’s time to consult an expert.
Warning Signs Indicating Professional Help
- Consistent Noise: If your freezer emits continuous loud noises like banging or rattling, it indicates potential mechanical failure.
- Temperature Irregularities: Noticeable fluctuations in temperature, where food frequently thaws and refreezes, signal a serious problem with the compressor.
- Burning Smell: A burning smell often points to electrical issues. This can be dangerous, so you should contact a technician immediately.
- Frequent Breakdowns: If your freezer requires constant resetting or if the compressor frequently cycles on and off, the issue may exceed DIY fixes.
- Frost Buildup: Excessive frost inside the freezer often means airflow is obstructed or the evaporator coil is malfunctioning.
- Check Credentials: Verify that the technician is licensed and insured. Look for certifications from recognized organizations in appliance repair.
- Read Reviews: Seek reviews and testimonials from past customers. Websites like Yelp and Google Reviews provide insight into the technician’s reliability and expertise.
- Get Estimates: Always ask for a detailed estimate before work begins. This ensures you understand potential costs and helps compare prices among technicians.
- Ask About Experience: Inquire how long the technician has specialized in deep freezer repairs. Those with extensive experience are more likely to diagnose issues accurately.
- Warranty Information: Confirm if the technician offers a warranty on labor and parts. This provides peace of mind in case the problem resurfaces shortly after repairs.
Understanding these signs and tips helps ensure you get the best service when dealing with compressor problems.
Conclusion
Dealing with a deep freezer compressor that isn’t working can be a real hassle. By staying alert to the signs and understanding the potential causes, you’re already on the right track to finding a solution. Regular maintenance like cleaning the condenser coils can make a big difference in keeping your freezer running smoothly.
If you find yourself overwhelmed or unsure of the next steps, don’t hesitate to reach out to a professional. Getting expert help can save you time and protect your food investments. Remember you’re not alone in this, and with a bit of troubleshooting, you can get your freezer back to its best.





Frequently Asked Questions
What are the common signs of a malfunctioning deep freezer compressor?
A malfunctioning deep freezer compressor may exhibit signs such as unusual noises (loud humming, clicking, or buzzing) and temperature fluctuations, where food items frequently thaw and refreeze. Monitoring these symptoms is crucial, as they can indicate potential compressor failure and lead to food spoilage if not addressed promptly.
What causes a deep freezer compressor to fail?
Compressor failure can occur due to electrical issues (like loose wiring), mechanical failures (wear and tear), or blocked condenser coils (which obstruct airflow). Identifying these causes helps in troubleshooting and resolving compressor issues efficiently, preventing further complications.
How can I troubleshoot my deep freezer’s compressor?
Start troubleshooting by checking the power supply to ensure the freezer is plugged in, the circuit breaker is not tripped, and the power cord is undamaged. Then, inspect the thermostat by adjusting settings and testing its continuity. Lastly, locate and clean condenser coils regularly to maintain optimal performance.
When should I call a professional for compressor issues?
You should contact a professional if you notice consistent loud noises, temperature irregularities, a burning smell, frequent breakdowns, or excessive frost buildup. These signs indicate serious issues that require expert assistance to prevent further damage or food loss.
How do I choose a qualified technician for compressor repairs?
To choose a qualified technician, check their credentials, read reviews, and obtain estimates. Ask about their experience with deep freezers, confirm warranty information, and ensure they are licensed. This due diligence helps ensure you receive reliable service for your compressor problems.
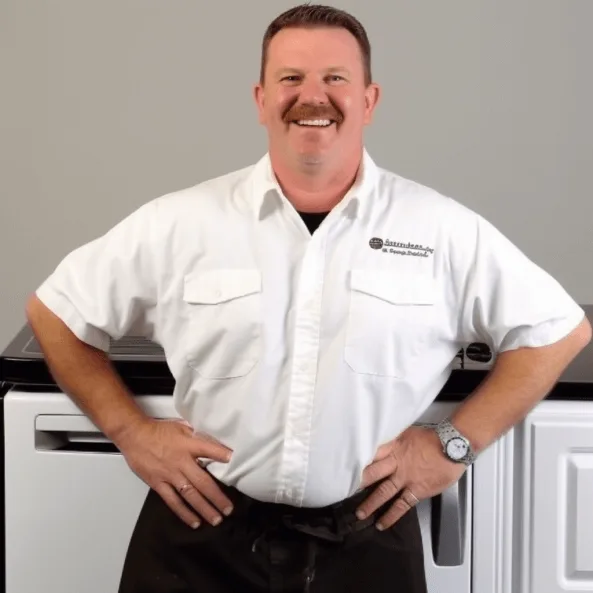
Hey, I’m Jake. I focus on cooling systems at Appliance Mastery, like fridges, freezers, and air conditioners.
I’ve worked in appliance repair for more than ten years and I’m certified through NASTeC. I’ve seen just about every fridge issue you can imagine.
My goal is to help you fix problems without stress. Whether it’s a freezer that won’t cool or an AC that keeps beeping, I’m here to walk you through it.