Have you ever reached for a glass of ice-cold water only to find your freezer ice maker isn’t working? It’s a frustrating moment that can leave you scratching your head. You might be wondering if it’s a simple fix or if you need to call in a professional.
Key Takeaways
- Common Causes: Freezer ice makers may stop working due to clogged water lines, faulty components, or electrical issues. Identifying the root cause is essential for effective troubleshooting.
- Power and Water Supply Checks: Always verify that the ice maker is receiving power and that the water supply is unobstructed. Check the power cord, circuit breaker, and any water inlet valves.
- Preventive Maintenance: Regular cleaning and monitoring of the temperature settings can help maintain your ice maker’s performance and longevity. Clean filters and remove mineral deposits to prevent issues.
- Signs for Professional Help: Look for red flags like persistent leaks, the ice maker not powering on, or unusual noises, which may indicate a more serious mechanical issue requiring professional assessment.
- Cost Awareness: Understanding potential repair costs helps in making informed decisions. Service calls and parts replacement can range significantly, so weigh the cost of repairs against the price of a new ice maker.
Common Causes of a Freezer Ice Maker Stopped Working
Several factors can lead to a freezer ice maker not functioning. Identifying the cause will help determine the right solution.
Mechanical Issues
- Clogged Water Line: Ice makers require a steady water supply. A clogged water line can hinder or stop water flow, preventing ice production. Check the line for kinks or blockages.
- Faulty Ice Maker Assembly: The ice maker components may malfunction. If the motor fails, the ice maker may not operate. Inspect for signs of wear or damage and consider replacing the faulty parts.
- Jammed Ice Movement: Ice can sometimes jam the mechanism that dispenses it. If you notice a block of ice in the tray, carefully remove it to restore normal function.
- Disconnected Power Supply: The ice maker needs electricity to function properly. Ensure it’s plugged in and the outlet is working. Check for tripped circuit breakers as well.
- Failed Thermostat: A malfunctioning thermostat can disrupt the ice maker’s temperature regulation. If the freezer is too warm, consider testing the thermostat’s resistance and replacing it if needed.
- Defective Control Board: The control board manages the ice-making process. If it fails, it can cause the ice maker to stop functioning. Testing the board for continuity or replacing it can resolve this issue.
Troubleshooting Steps
When your freezer ice maker stops working, follow these troubleshooting steps to identify and fix the issue.
Checking Power Supply
Ensure the ice maker receives power. Check the following:
- Power Cord: Verify it’s securely plugged into an outlet.
- Circuit Breaker: Inspect the breaker for tripped switches. Reset if needed.
- Ice Maker Switch: Confirm the ice maker’s power switch is on. Some models have a separate switch.
Testing with a multimeter can help measure voltage if necessary.
Inspecting Water Supply
A lack of water can cause ice makers to malfunction. Here’s what to check:
- Water Line: Look for kinks or obstructions in the water line. Straighten any bends.
- Water Valve: Check the water inlet valve for openings. Ensure it functions correctly.
- Filter: If your system includes a filter, inspect it for clogs. Replace it if it’s dirty or overdue for a change.
Monitoring the water supply can pinpoint many common issues with ice makers.
Preventive Maintenance Tips
You can maintain your freezer ice maker to prevent future issues. Regular check-ups and adjustments keep your ice maker running smoothly.
Regular Cleaning
Cleaning your ice maker is crucial. Water and ice can accumulate mineral deposits and debris over time. Here’s how to keep it clean:
- Unplug the Ice Maker: Safety first. Disconnect it from the power source before cleaning.
- Remove Ice and Water: Dispose of any remaining ice and drain excess water from the reservoir.
- Wipe Down Surfaces: Use a mild detergent solution to clean the interior and exterior surfaces. Avoid abrasive cleaners that can scratch or damage components.
- Check and Clean Filters: Inspect water filters regularly. Replace or clean them every six months or as recommended by the manufacturer.
Temperature Settings
Temperature plays a significant role in ice production. Here are some steps to ensure optimal settings:
- Set the Freezer Temperature: Maintain the freezer temperature between 0°F and 5°F (-18°C to -15°C) for efficient ice production.
- Avoid Overloading: Don’t overcrowd the freezer, as this can block airflow and affect temperature stability.
- Monitor Environmental Factors: Keep the freezer away from heat sources, like ovens or direct sunlight. External heat can cause temperature fluctuations.
By following these preventive maintenance tips, you can keep your freezer ice maker in top shape and minimize the chances of malfunction.
When to Call a Professional
Determining whether to call a professional can save time and money. Recognizing the right signs helps you decide when it’s essential to seek expert assistance.
Signs of a Major Issue
Look for specific indicators that suggest a serious problem with your ice maker.
- Ice Maker Won’t Power On: If troubleshooting shows no power and the outlet works with other devices, consider a deeper electrical fault.
- Frequent Water Leaks: Persistent leaks might signal a malfunctioning water inlet valve or a crack in the water line, requiring professional evaluation.
- Ice Appears Cloudy or Discolored: If ice lacks clarity, it could indicate water contamination, hinting at broader plumbing issues.
- Continuous Running Noise: Unusual sounds from the ice maker may suggest internal mechanical problems that a technician should inspect.
Cost Considerations
Understanding potential costs can help you prepare for professional services.
- Service Call Fees: On average, service calls range from $50 to $150, varying by location and availability.
- Parts Replacement: Component costs can add up, with parts like the water inlet valve costing around $30 to $100 and control boards upwards of $150.
- Total Repair Costs: Expect total repair expenses between $100 and $400, depending on labor and part requirements.
- Cost vs. Replacement: If repair costs exceed 50% of a new ice maker, replacing the unit might be more economical.
Being informed about these signs and costs helps you make a timely decision when your ice maker stops working.
Conclusion
Dealing with a malfunctioning ice maker can be frustrating but you don’t have to let it ruin your day. By following the troubleshooting steps and maintenance tips outlined in this article you can often get your ice maker back up and running in no time.
If you find yourself facing persistent issues or signs of major problems don’t hesitate to reach out to a professional. Remember that understanding the potential costs can help you make the best decision for your situation. With a little patience and effort you can enjoy refreshing ice-cold drinks again soon.
Frequently Asked Questions
What are common causes for a malfunctioning ice maker?
A malfunctioning ice maker can be caused by several issues, including a clogged water line, faulty ice maker assembly, jammed ice movement, disconnected power supply, failed thermostat, or a defective control board. Identifying these problems can help determine the next steps.
How can I troubleshoot my ice maker?
Start by checking the power supply to ensure the ice maker is plugged in and the power switch is on. Next, inspect the water line for kinks and verify the water inlet valve is functioning. Also, check that filters are clean and not clogged.
When should I clean my ice maker?
Regular cleaning is recommended to prevent build-up of mineral deposits and debris. Clean your ice maker every few months or whenever you notice signs of malfunction. Make sure to unplug it before cleaning and use a mild detergent.
What temperature should I keep my freezer for optimal ice production?
To ensure proper ice production, keep your freezer temperature between 0°F and 5°F (-18°C to -15°C). This helps maintain the ice maker’s efficiency and prevents potential malfunctions.
How do I know if I need professional help for my ice maker?
Signs that indicate the need for professional assistance include the ice maker not powering on, frequent water leaks, cloudy or discolored ice, and unusual running noises. If these issues persist, consider contacting a technician.
What costs should I expect when hiring a professional for ice maker repairs?
Costs can vary depending on the issue but typically include service call fees, parts replacement, and overall repair expenses. If repair costs exceed 50% of a new ice maker, it may be more economical to replace it instead.
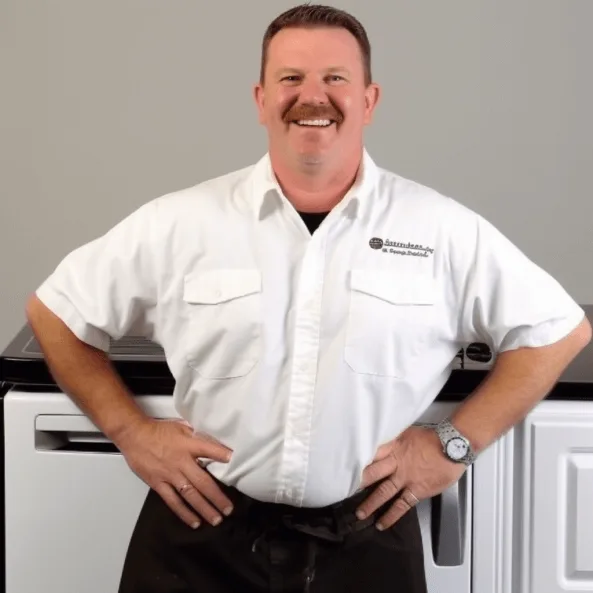
Hey, I’m Jake. I focus on cooling systems at Appliance Mastery, like fridges, freezers, and air conditioners.
I’ve worked in appliance repair for more than ten years and I’m certified through NASTeC. I’ve seen just about every fridge issue you can imagine.
My goal is to help you fix problems without stress. Whether it’s a freezer that won’t cool or an AC that keeps beeping, I’m here to walk you through it.