Is your Frigidaire Gallery freezer’s ice maker giving you the cold shoulder? You’re not alone. Many people face this frustrating issue, especially when you’re hosting friends or just craving a cool drink on a hot day.
Key Takeaways
- Common Issues: Ice maker problems include lack of ice production and ice jams, often caused by low freezer temperatures or blockages in the water supply line.
- Essential Troubleshooting: Check power supply connections, inspect water lines for kinks, and ensure ice maker components like the ice bin and auger are clear to maintain optimal operation.
- Maintenance Tips: Clean the ice maker every six months and keep the freezer temperature below 0°F (-18°C) to enhance performance and ice quality.
- When to Seek Help: Persistent issues, unusual noises, water leaks, or poor ice quality may require professional evaluation and repairs from certified technicians.
Common Issues With Frigidaire Gallery Freezer Ice Makers
Many users encounter specific issues with the ice maker in their Frigidaire Gallery freezer. Identifying these problems early can save time and frustration.
Lack of Ice Production
Lack of ice production frequently occurs due to various factors. Ensure the freezer temperature is set below 0°F (-18°C). Check the water supply line for kinks or blockages. It’s also wise to inspect the filter for clogs, which can restrict water flow. If you’ve recently moved the unit, allow 24 hours for the ice maker to begin producing ice after reconnecting the water supply.
Ice Maker Jam
Ice maker jams often result from ice clumps blocking the mechanism. Empty the ice bin regularly to prevent overflow and improve operational efficiency. Use a warm cloth to gently melt ice buildup around the components. Ensure that the ice maker arm isn’t stuck in a raised position, as this can interrupt the ice-making cycle. If the problem persists, consult the user manual for specific troubleshooting steps.
Troubleshooting Steps
Fixing the ice maker on your Frigidaire Gallery freezer involves a few straightforward steps. Follow these actions to identify and resolve common issues.
Checking Power Supply
Confirm the ice maker has power. Check the following:
- Plug Connection: Ensure the freezer’s plug is securely connected to the outlet.
- Circuit Breaker: Check your home’s circuit breaker for any tripped switches.
- Power Settings: Make sure the ice maker switch is in the “on” position.
If these steps don’t resolve the issue, try resetting the unit. Unplug it for about 10 minutes, then plug it back in.
Inspecting Water Supply
Ice production depends on a steady water supply. Verify these components:
- Water Line: Look for kinks or blockages in the water supply line. Straighten any bends and check for obstructions.
- Water Inlet Valve: Make sure the water inlet valve is functioning. It should open when the ice maker requests water.
- Filter Status: Examine the water filter. A clogged filter can restrict flow, so replace it if necessary.
If there’s no water flowing, consider running some water through the line to clear any blockages.
Examining Ice Maker Components
Inspect these critical components in the ice maker:
- Ice Bin: Empty the ice bin regularly to prevent jams. Excess ice can block new production.
- Auger: Check the auger for blockages. Clear any ice stuck in the auger to facilitate movement.
- Ice Maker Arm: Ensure the ice maker arm isn’t stuck or caught on anything. The arm should move freely to signal ice production.
If problems continue after these checks, consulting the user manual for specific troubleshooting instructions is beneficial.
Maintenance Tips for Ice Makers
Keeping your ice maker in top shape ensures consistent ice production. Regular maintenance helps prevent many common issues users face.
Regular Cleaning Procedures
- Clean the ice maker every six months. This prevents mold and mineral buildup.
- Remove any ice from the bin before cleaning.
- Use a gentle detergent and warm water to wipe down surfaces.
- Rinse thoroughly with warm water to remove any soap residue.
- To clean the water supply line, disconnect it and flush it with water.
- Check and clean the water filter to enhance ice quality and taste.
- Set your freezer temperature below 0°F (-18°C) for optimal ice production.
- Regularly check the temperature with a thermometer. Freezers can fluctuate, affecting ice yields.
- If ice production slows, adjust the thermostat. Make increments of 1°F and monitor changes.
- Avoid placing warm items in the freezer. This raises the internal temperature and disrupts ice formation.
- Allow 24 hours after adjusting settings for the ice maker to stabilize and start producing again.
Following these maintenance tips helps ensure your Frigidaire Gallery freezer’s ice maker functions smoothly, providing ice whenever you need it.
When to Call a Professional
If troubleshooting steps haven’t resolved the ice maker issue, it’s time to consider contacting a professional technician. Certain signs can indicate the need for expert help.
- Persistent Issues: If the ice maker still doesn’t produce ice after checking the power supply, water supply, and ice maker components, a professional can diagnose more complex problems.
- Strange Noises: Unusual sounds coming from the ice maker can signal mechanical failures. Technicians can assess internal components and repair or replace them as needed.
- Water Leaks: If you notice water pooling or leaking around the ice maker, this could point to serious plumbing issues that require professional assistance.
- Electrical Problems: Fluctuating power or issues with the ice maker switch may indicate electrical faults. Professionals can ensure safety during electrical repairs.
- Frequent Jams: Frequent or severe ice jams, despite regular maintenance and cleaning, can suggest a defect in the ice maker mechanism. An expert can provide specialized repairs.
- Ice Quality Issues: If the ice produced is discolored, has strange odors, or tastes off, this may indicate a problem with the water supply or filtration system. A technician can evaluate and resolve these concerns.
You should schedule repairs with certified technicians to ensure proper repairs and adherence to safety standards.
Conclusion
Dealing with a malfunctioning ice maker can be annoying but you’re not alone in this. By following the troubleshooting tips and maintenance advice shared, you can get your Frigidaire Gallery freezer’s ice maker back on track. Remember to check the basics like the power supply and water line before diving deeper into repairs.
If you find yourself still facing issues after trying everything, don’t hesitate to reach out to a professional. Keeping your ice maker in good shape means more refreshing drinks and less stress during those warm gatherings. With a little care and attention, you’ll be enjoying ice right when you need it.
Frequently Asked Questions
What common problems occur with the Frigidaire Gallery freezer’s ice maker?
Many users face issues such as ice production failures and ice maker jams. These problems can hinder ice availability during gatherings or hot days.
How can I fix a lack of ice production in my ice maker?
Ensure the freezer temperature is below 0°F (-18°C). Check for kinks or blockages in the water supply line, and inspect the filter for clogs. If recently moved, wait 24 hours for ice production to resume.
What should I do to resolve ice maker jams?
Regularly empty the ice bin to avoid overflow and use a warm cloth to melt any ice buildup. Additionally, ensure the ice maker arm isn’t stuck.
How do I check the power supply for my ice maker?
Verify that the ice maker plug is securely connected, the circuit breaker is not tripped, and the ice maker switch is turned on.
What maintenance tips should I follow for my ice maker?
Clean the ice maker every six months using gentle detergent and warm water. Regularly check the freezer temperature, avoid placing warm items inside, and allow 24 hours for the unit to stabilize after any adjustments.
When should I contact a professional technician?
Consider calling a technician if you experience ongoing ice production issues, strange noises, water leaks, electrical problems, frequent jams, or poor ice quality despite troubleshooting efforts.
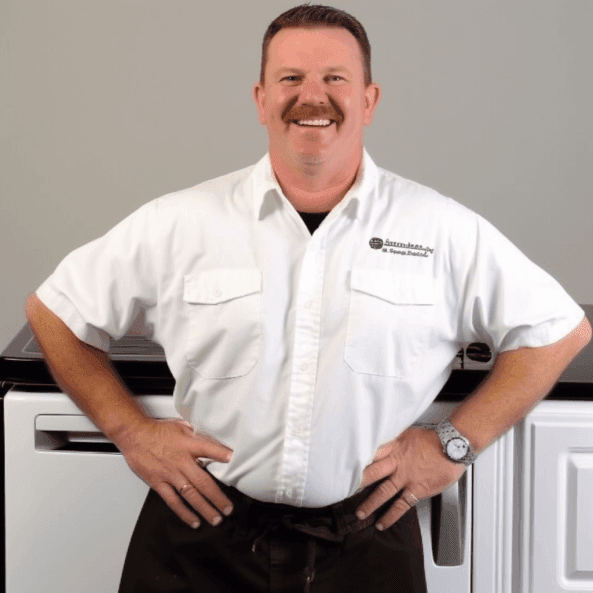
Jake Newman is Appliance Mastery’s expert on refrigeration and cooling systems. With over a decade of experience in the appliance repair industry and certification from NASTeC, Jake is a trusted source of knowledge for homeowners who want to troubleshoot and repair their fridges, freezers, and air conditioning units.