Have you ever reached for a glass of ice only to find your GE bottom freezer ice maker isn’t working? It’s frustrating, especially when you’re hosting friends or just want to cool off with a refreshing drink. You’re not alone—many people encounter this issue, and it can feel overwhelming when you don’t know where to start.
Key Takeaways
- Common Issues: GE bottom freezer ice makers often face problems like water supply blockages, clogged filters, and faulty thermostats that can stop ice production.
- Signs of Malfunction: Look for indicators such as no ice production, small or hollow ice cubes, and ice sticking in the tray to identify malfunctions early.
- Troubleshooting Steps: Start troubleshooting by checking the power supply, water line connections, and temperature settings to ensure optimal operation.
- DIY Repair Tips: Inspect and clean components, replace clogged filters, and manually activate the ice maker to resolve simple issues without professional help.
- Maintenance Recommendations: Regular cleaning and seasonal maintenance enhance the efficiency and longevity of your ice maker, preventing potential issues.
- Professional Help: For persistent problems or complex repairs, consult a professional to avoid voiding warranties and ensure safe handling of mechanical issues.
Common Issues with GE Bottom Freezer Ice Makers
GE bottom freezer ice makers can encounter several issues that hinder their performance. Understanding these problems helps you troubleshoot effectively and ensures your ice maker works smoothly when you need it most.
Understanding Ice Maker Mechanics
Ice makers operate through a series of components working together. The water inlet valve fills the ice tray with water. A thermostat detects the temperature and signals when to freeze or eject ice. If any of these components malfunction, ice production stops. Common mechanical issues include:
- Water supply blockage: Check the water line for kinks or ice buildup.
- Clogged filter: Replace water filters regularly to maintain a clear flow.
- Faulty thermostat: A broken thermostat won’t signal ice production, leading to a dry ice maker.
Signs of a Malfunctioning Ice Maker
Recognizing the signs of a malfunctioning ice maker can help you address the problem quickly. Common indicators include:
- No ice production: If the ice maker hasn’t produced ice for a few hours.
- Small or hollow ice cubes: This can indicate insufficient water supply or a clogged filter.
- Ice sticking in the tray: If the ice doesn’t release easily, it might signal a problem with the ejector arm or the heater.
Addressing these issues promptly can restore your ice maker’s functionality and ensure you always have ice on hand for your needs.
Troubleshooting Steps for GE Bottom Freezer Ice Maker
If your GE bottom freezer ice maker isn’t working, follow these troubleshooting steps to identify and resolve the issue quickly.
Checking Power Supply and Settings
- Verify it’s plugged in. Ensure the power cord is securely connected to a functioning outlet.
- Confirm the power switch is on. Look for the power switch on the ice maker and make sure it’s turned on.
- Inspect the circuit breaker. An overloaded circuit might trip the breaker. Reset the breaker if necessary.
- Check temperature settings. Ice makers typically operate best at temperatures below 0°F (-18°C). Ensure the freezer temperature is correctly set.
- Examine the water line connection. Ensure the water supply line is securely attached to the back of the refrigerator.
- Check for kinks or blockages. Inspect the water line for any kinks or signs of obstruction that may restrict water flow.
- Replace the water filter. A clogged water filter can obstruct water flow to the ice maker. Change the filter if it hasn’t been replaced in the past six months.
- Test the water inlet valve. The water inlet valve controls water flow to the ice maker. Use a multimeter to check for continuity. Replace the valve if it’s faulty.
Repair and Replacement Options
If your GE bottom freezer ice maker isn’t working, various repair and replacement options are available to restore its function.
DIY Repair Tips
- Inspect Components: Check the water inlet valve for blockages or damage. Ensure the valve is open and supplying water to the ice maker.
- Clear Clogs: Clean the water filter if water flow seems restricted. Replace it if it’s overdue for a change.
- Adjust Temperature: Verify that the freezer is set below 0°F (-18°C). Adjust settings if necessary to encourage ice production.
- Test the Ice Maker: Manually activate the ice maker by pressing the reset button. Refer to your user manual for the exact location of the button.
- Check for Ice Buildup: Remove any visible ice obstructing the ice tray or mechanisms. Defrost if needed to clear blockages.
- Persistent Issues: If the ice maker doesn’t respond after DIY attempts, a professional evaluation might be necessary.
- Complex Repairs: Issues involving the ice maker’s wiring, control board, or sealed system often require trained technicians.
- Warranty Considerations: If your appliance is under warranty, consult a professional to avoid voiding coverage from any DIY fixes.
- Safety Concerns: If you detect unusual odors, leaks, or hear unusual noises, these signals often indicate deeper mechanical problems best suited for professionals.
Maintenance Tips for Optimal Performance
Proper maintenance enhances your GE bottom freezer ice maker’s efficiency and longevity. Follow these practical tips to ensure smooth operation.
Regular Cleaning Procedures
Regularly clean your ice maker to prevent buildup and ensure optimal performance. Clean the ice bin and exterior every month with warm, soapy water. Rinse thoroughly and dry. Every six months, check and clean the water inlet valve and any accessible filters. If your ice maker supports it, use a vinegar solution to eliminate mineral deposits. Regular cleaning boosts ice quality and prevents blockages.
Seasonal Maintenance Guidelines
Seasonal maintenance keeps your ice maker running efficiently year-round. Before winter, inspect the water lines for leaks and ensure the water supply is disconnected if not in use. In the spring, check the seals and gaskets for wear and tear, replacing them if necessary. During warmer months, ensure the freezer’s temperature stays consistently below 0°F (-18°C) to support proper ice production. Regular season checks help avoid major issues down the road.
Conclusion
Dealing with a malfunctioning ice maker can be a real hassle but you’ve got the tools to tackle it. Remember to keep an eye on those common issues and follow the troubleshooting steps to get things back on track. Regular maintenance is key to preventing future problems and ensuring your ice maker runs smoothly.
If you find yourself stumped don’t hesitate to reach out for professional help. You deserve a reliable supply of ice for all your gatherings and everyday needs. With a little patience and care your ice maker can be a dependable part of your kitchen again.
Frequently Asked Questions
What causes my GE bottom freezer ice maker to stop working?
Ice makers can stop functioning due to several reasons, including water supply blockages, clogged filters, thermostat issues, or electrical problems. It’s essential to check these components to identify the root cause.
How do I know if my ice maker is malfunctioning?
Signs of a malfunctioning ice maker include no ice production, small or hollow ice cubes, and ice sticking in the tray. If you notice any of these symptoms, it’s time to troubleshoot.
What troubleshooting steps should I take if my ice maker isn’t making ice?
First, ensure the unit is plugged in and the power switch is on. Check that the freezer temperature is set below 0°F (-18°C). Inspect the water line for kinks, replace clogged filters, and test the water inlet valve.
Can I fix my ice maker myself, or do I need a professional?
You can try DIY repairs by inspecting components, clearing clogs, or adjusting the temperature settings. However, if the problem persists—especially with wiring or control boards—consult a professional for help.
How can I maintain my GE bottom freezer ice maker?
To maintain optimal performance, clean the ice bin and exterior monthly, and check the water inlet valve and filters every six months. Inspect water lines for leaks seasonally to prevent future issues.
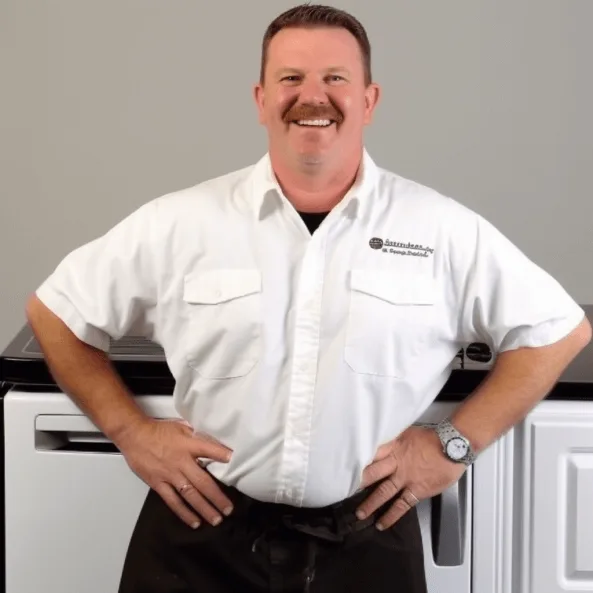
Hey, I’m Jake. I focus on cooling systems at Appliance Mastery, like fridges, freezers, and air conditioners.
I’ve worked in appliance repair for more than ten years and I’m certified through NASTeC. I’ve seen just about every fridge issue you can imagine.
My goal is to help you fix problems without stress. Whether it’s a freezer that won’t cool or an AC that keeps beeping, I’m here to walk you through it.