Is your GE Profile bottom freezer ice maker refusing to make ice? You’re not alone. Many people face this frustrating issue, especially when they need ice for a party or a refreshing drink.
Understanding why your ice maker isn’t working can save you time and money. Whether it’s a simple fix or a sign of a bigger problem, this article will guide you through common causes and solutions. By the end, you’ll be equipped to tackle the issue and hopefully enjoy ice-cold beverages again in no time.
Key Takeaways
- Common Issues: Mechanical problems like clogged water lines, faulty assemblies, ice blockages, and incorrect temperatures are frequent causes of ice maker malfunctions.
- Electrical Troubleshooting: Electrical issues including power supply problems, faulty sensors, and timer malfunctions can prevent the ice maker from working properly.
- Effective Troubleshooting Steps: Check the water supply, inspect the ice maker assembly, clear any blockages, and validate electrical connections to diagnose problems efficiently.
- Regular Maintenance: Clean the ice maker every six months and conduct inspections to identify any potential issues early on, ensuring optimal performance.
- User Experiences: While many appreciate the convenience and reliability of the ice maker, common complaints often revolve around ice production gaps and temperature fluctuations. Understanding these can help identify solutions.
Common Issues With GE Profile Bottom Freezer Ice Maker
Understanding common issues with the GE Profile bottom freezer ice maker helps you troubleshoot effectively. Several factors contribute to ice maker malfunctions, primarily related to mechanical and electrical problems.





Mechanical Problems
Mechanical issues often prevent the ice maker from functioning. Here are some common mechanical problems to check:
- Clogged Water Line: Ice makers need a steady water supply. Inspect the water line for kinks or clogs that may restrict flow. Clear any obstructions.
- Faulty Ice Maker Assembly: The ice maker assembly includes various components like the motor and gears. A malfunctioning motor can stop ice production. Test the ice maker unit for any signs of damage or wear.
- Ice Blockage: Sometimes ice builds up and obstructs the ice maker. Defrost the unit and remove any obstructions to restore proper functioning.
- Incorrect Temperature: The freezer should maintain a temperature below 0°F (-18°C). Use a thermometer to check the temperature and adjust the thermostat if necessary.
Electrical Problems
Electrical issues can also impede the ice maker’s operation. Consider these common electrical problems:
- Power Supply Issues: Ensure the ice maker is plugged in and the outlet is functioning. If the outlet isn’t working, check the circuit breaker for any tripped switches.
- Faulty Sensors: Ice makers have sensors that monitor ice production. If these sensors malfunction, ice making may stop. Test the sensors for electrical continuity and replace them if faulty.
- Timer Malfunction: The ice maker relies on a timer to control the ice-making cycle. If the timer is defective, it may prevent the ice maker from cycling correctly. Check and replace the timer as needed.
By identifying these common issues with the GE Profile bottom freezer ice maker, you can take steps to resolve them quickly and efficiently.
Troubleshooting Steps
When your GE Profile bottom freezer ice maker isn’t working, a few troubleshooting steps can help you identify and fix the issue. Follow these actions to get your ice maker back on track.
Check Water Supply
- Examine Water Line: Inspect the water line for kinks or blockages that could hinder water flow. Ensure it’s properly connected to the ice maker.
- Verify Water Valve: Make sure the water supply valve is open. If it’s closed, your ice maker won’t receive water.
- Test Water Pressure: Low water pressure may affect ice production. If the pressure seems low, consider checking plumbing connections or filters for obstructions.
- Replace Water Filter: If your ice maker features a water filter, check its status. A clogged filter can significantly reduce water flow. Replace it if necessary.
- Check Ice Maker Assembly: Inspect the ice maker assembly for damage or wear. A malfunctioning assembly may require replacement.
- Look for Ice Blockages: Remove any ice blockages from the ice maker and the ice bin. Ice buildup can prevent new ice from forming.
- Test the Ice Level Sensor: Ensure the ice level sensor functions correctly. If it’s stuck or malfunctioning, it can disrupt the ice-making process.
- Validate Electrical Connections: Inspect the wiring and connections to the ice maker. Loose or damaged wires can cause electrical issues that prevent operation.
By following these steps, you can effectively troubleshoot common issues with your GE Profile bottom freezer ice maker, facilitating a quick and efficient resolution.





Maintenance Tips
Regular maintenance ensures your GE Profile bottom freezer ice maker runs efficiently and produces ice as expected. Follow these tips for optimal performance.
Cleaning the Ice Maker
Cleaning the ice maker promotes better ice production and improves hygiene. Start by unplugging the refrigerator. Then, remove any ice that’s in the bin. Use a mixture of warm water and mild soap to clean the ice maker’s interior. Wipe down the ice trays with a soft cloth. Rinse with clean water and ensure no soap residue remains. Additionally, clean the exterior and the ice bin to remove any spills or dust. Perform this cleaning every six months for best results.
Regular Inspections
Regular inspections help identify potential issues before they escalate. Check the water line for any kinks or blockages. Look for leaks around the ice maker and under the fridge. Examine the ice maker assembly for signs of damage or wear. Ensure that the freezer temperature stays between 0°F and 5°F. Check the water supply valve to confirm it’s open. Schedule these inspections every few months to maintain ice maker functionality and performance.
Customer Experiences
Many users share their experiences with the GE Profile bottom freezer ice maker, highlighting both positive feedback and common complaints.
Positive Feedback
Users appreciate the convenience and efficiency of having a bottom freezer ice maker. Many report that when functioning properly, the ice maker produces a steady supply of ice. Positive experiences include:





- Easy Access: Bottom-freezer designs allow easy access to ice and food without bending.
- Quiet Operation: Many find the ice maker operates quietly compared to other models.
- Sleek Design: Users often mention their satisfaction with the modern look and feel of GE Profile appliances.
- Reliable Performance: When well-maintained, some users report years of dependable ice production without major issues.
Common Complaints
Despite its advantages, several users encounter issues that impact their ice maker’s performance. Common complaints include:
- Ice Production Gaps: Some experience intermittent ice production, often due to water supply issues or blockages.
- Ice Blockages: Users frequently report ice blocks forming, which hinder normal operation and require manual clearing.
- Temperature Fluctuations: Many mention that incorrect freezer temperatures affect ice quality and production rates.
- Water Line Problems: Complaints about kinks or leaks in water lines often arise, which can disrupt the water supply needed for ice making.
Understanding these experiences can help you identify potential problems and solutions for your own GE Profile bottom freezer ice maker.
Conclusion
Dealing with a malfunctioning ice maker can be frustrating but you’re not alone. By understanding the common issues and following the troubleshooting steps outlined, you can get your GE Profile bottom freezer ice maker back on track. Remember that regular maintenance is key to preventing future problems and keeping your ice maker running smoothly.
If you take the time to inspect and care for your appliance, you’ll enjoy ice-cold beverages whenever you need them. Don’t hesitate to reach out for professional help if the problem persists. Happy ice making!
Frequently Asked Questions
Why is my GE Profile bottom freezer ice maker not producing ice?
The ice maker may not produce ice due to clogged water lines, a faulty water valve, or low water pressure. Check the water supply and ensure there are no blockages. It’s also essential to inspect the ice maker assembly and confirm the freezer temperature is set correctly.
How can I troubleshoot my ice maker?
To troubleshoot, check the water line for kinks or clogs, verify that the water valve is open, and ensure the water filter isn’t clogged. Additionally, inspect the ice maker assembly for damage and test the ice level sensor.
What are common causes of ice maker malfunctions?
Common causes include clogged water lines, incorrect freezer temperatures, faulty water valves, and power supply issues. Mechanical problems, such as ice blockages and defective sensors or timers, can also affect the ice maker’s performance.
How can I maintain my ice maker for better performance?
Regularly clean the ice maker and inspect it for potential issues. Check the water supply line, look for leaks, and ensure the freezer temperature is consistently maintained to enhance functionality and longevity.
What should I do if the ice maker has blockages?
If you notice blockages, carefully remove any ice clumps and ensure there are no obstructions in the ice maker assembly or water line. Regular maintenance can help prevent future blockages.
Is it necessary to replace the water filter regularly?
Yes, replacing the water filter regularly is crucial as a clogged filter can significantly impact water flow and ice production. Follow the manufacturer’s guidelines on replacement frequency for optimal performance.
What do users typically say about the GE Profile ice maker?
Users generally appreciate the ice maker’s convenience, efficiency, and sleek design. However, some report issues like intermittent ice production and temperature fluctuations, highlighting the importance of regular maintenance.
Can electrical issues affect ice maker performance?
Yes, electrical issues such as faulty connections or timers can impede the ice maker’s operation. Inspect all electrical components to ensure they are functioning properly for optimal ice production.
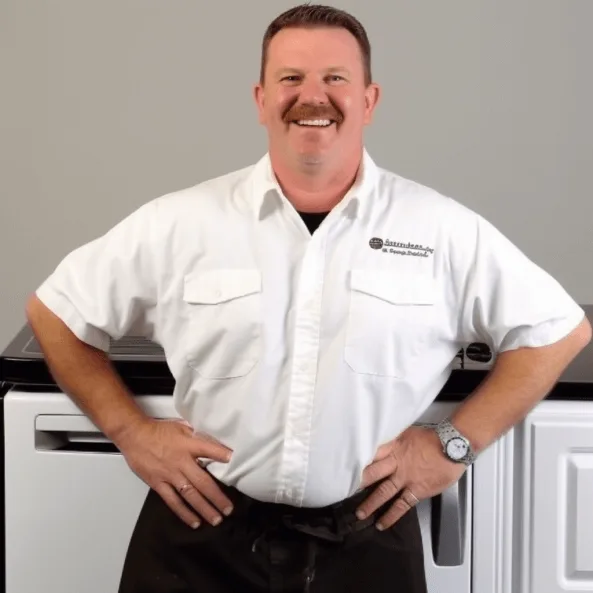
Hey, I’m Jake. I focus on cooling systems at Appliance Mastery, like fridges, freezers, and air conditioners.
I’ve worked in appliance repair for more than ten years and I’m certified through NASTeC. I’ve seen just about every fridge issue you can imagine.
My goal is to help you fix problems without stress. Whether it’s a freezer that won’t cool or an AC that keeps beeping, I’m here to walk you through it.