Have you ever faced a sudden power outage only to find your Generac generator flashing an error code? It’s frustrating, especially when you rely on it for backup power. The Generac 2800 error code can leave you scratching your head, wondering what went wrong and how to fix it.
Key Takeaways
- Understanding the 2800 Error Code: This error typically indicates fuel-related issues, including low fuel levels, clogged filters, or faults in the fuel pump.
- Common Causes: Key factors triggering the 2800 error include low fuel, clogged fuel filters, air in fuel lines, electrical issues (e.g., loose connections or battery problems), and neglected maintenance.
- Troubleshooting Steps: Essential steps for troubleshooting include checking fuel levels, inspecting the fuel filter, bleeding air from fuel lines, and examining electrical connections and battery condition.
- Routine Maintenance: Regular maintenance, such as changing oil, replacing filters, and conducting periodic inspections, is crucial for preventing error codes and ensuring generator reliability.
- When to Seek Help: If DIY troubleshooting fails, consult a licensed technician for complex issues or major repairs to ensure your generator operates safely and effectively.
Understanding Generac Generator 2800 Error Code
Encountering the 2800 error code on your Generac generator can feel overwhelming, especially during a power outage. This code typically indicates a fuel issue, often related to fuel delivery or low fuel levels.
Common Causes of the 2800 Error Code
- Low Fuel Levels
Check your generator’s fuel tank. Low fuel can prevent the generator from starting or operating efficiently. - Clogged Fuel Filter
Inspect the fuel filter for blockages. A clogged filter restricts fuel flow, leading to operational failures. - Air in the Fuel Lines
Air in the fuel lines disrupts fuel delivery. This can occur if the generator has been running low on fuel. - Faulty Fuel Pump
Confirm the fuel pump is functioning correctly. A malfunctioning pump may not deliver fuel adequately.
Troubleshooting Steps
- Check Fuel Level
Ensure the tank is at least one-quarter full. Fill it with the appropriate fuel type if levels are low. - Inspect Fuel Filter
Replace the fuel filter if it appears dirty or clogged. - Bleed the Fuel Lines
Follow the manufacturer’s guidelines to bleed air from the lines. This allows for smooth fuel delivery. - Test the Fuel Pump
If issues persist, evaluate the fuel pump’s operation. Consult a technician if unfamiliar with the process.
When to Seek Professional Help
If you troubleshoot these issues and still face the 2800 error code, consulting a licensed technician is advisable. They possess the expertise to diagnose and fix more complex problems, ensuring your generator operates safely and effectively.





Common Causes of Error Code
Encountering the 2800 error code on your Generac generator often points to specific issues. Understanding these common causes can help you troubleshoot effectively.
Fuel Issues
Fuel problems frequently trigger the 2800 error code. Check for these factors:
- Low Fuel Levels: Ensure your generator has sufficient fuel. Even a slight dip can lead to engine failure.
- Clogged Fuel Filter: Inspect the fuel filter for blockages. A clean filter allows fuel to flow freely.
- Air in Fuel Lines: Bleed the fuel lines if you suspect air has gotten in. Doing this restores proper fuel delivery.
- Faulty Fuel Pump: Test the fuel pump to see if it’s functioning correctly. A malfunction can prevent fuel from reaching the engine.
Electrical Problems
Electrical issues can also trigger the error code. Look for these common problems:
- Loose Connections: Examine all electrical connections. Loose or corroded connections can disrupt power supply.
- Battery Issues: Check the battery voltage. A low or dead battery won’t provide enough power to start the generator.
- Faulty Sensors: Inspect the sensors for any defects. Malfunctioning sensors can send incorrect signals to the generator’s control module.
Maintenance Neglect
Neglecting regular maintenance can lead to the 2800 error code. Consider these maintenance aspects:
- Oil Changes: Change the engine oil regularly. Old or contaminated oil can cause significant engine problems.
- Filter Changes: Replace air and fuel filters as needed. Dirty filters can impede performance and lead to error codes.
- Routine Inspections: Perform periodic checks on the generator. Address any signs of wear or potential issues before they escalate.
By addressing these common causes, you can troubleshoot the 2800 error code effectively, ensuring your Generac generator operates smoothly when you need it most.





Troubleshooting Steps
Troubleshooting your Generac generator after encountering a 2800 error code involves a few crucial steps. Follow these guidelines to identify and address common issues.
Checking Fuel Supply
- Verify Fuel Levels: Check the fuel gauge to ensure it’s not below the minimum level. Low fuel can trigger the 2800 error.
- Inspect for Leaks: Look for signs of fuel leaks around the generator. Fuel leaks can lead to inadequate supply.
- Clear Blockages: Examine the fuel filter for clogs. A dirty filter restricts fuel flow, causing performance issues.
- Test Fuel Quality: Assess the fuel quality. Old or contaminated fuel can impede the generator’s operation. Replace any stale fuel with fresh gasoline.
Inspecting Electrical Connections
- Examine Wiring: Inspect all wiring connected to the generator. Loose or frayed wires can disrupt power delivery.
- Check Battery Condition: Test the battery for charge and proper connections. A weak battery could result in operational failures.
- Tighten Connections: Secure all electrical connections. Ensuring they are tight can resolve many electrical-related issues.
- Look at Sensors: Inspect sensors for damage or misalignment. Faulty sensors can trigger erroneous error codes.
- Change Engine Oil: Perform oil changes regularly as per the manufacturer’s recommendations. Clean oil is vital for efficient engine operation.
- Replace Filters: Change the air and fuel filters to prevent blockages. Filters should be inspected and replaced at least once per year.
- Schedule Inspections: Conduct routine inspections, including checking belts and hoses. Regular checks can prevent minor issues from escalating.
- Run the Generator: Exercise the generator monthly by running it for at least 30 minutes. Regular use keeps components lubricated and operational.
By following these troubleshooting steps, you can effectively address the 2800 error code and enhance your generator’s reliability during power outages.
Solutions for Error Code
Encountering the 2800 error code on your Generac generator can be frustrating, but several practical solutions exist. Follow these troubleshooting steps to identify and resolve the issue effectively.
DIY Fixes
- Check Fuel Levels: Ensure the fuel tank is filled to the appropriate level. A low fuel level often triggers error code 2800.
- Inspect the Fuel Filter: Remove the fuel filter and check for clogs. Replace it if necessary to ensure proper fuel flow.
- Bleed the Fuel Lines: Release any air trapped in the fuel lines. This process restores fuel delivery to the engine.
- Test the Fuel Pump: Use a multimeter to measure the fuel pump’s voltage. If the voltage is below specifications, consider replacing the pump.
- Examine Electrical Connections: Check for loose or corroded connections. Tighten or clean them to improve electrical flow.
- Persistent Error Code: If none of the DIY fixes resolve the issue, seek assistance from a licensed technician. Complex problems may require specialized knowledge.
- Electrical Issues: If you notice ongoing electrical problems, such as battery faults or sensor failures, professional assessment ensures safety and reliability.
- Major Repairs Needed: When repairs to internal components arise, a technician can provide a thorough diagnosis and safe repairs that you might not handle alone.
By following these steps, you can address the Generac generator 2800 error code confidently and maintain your generator for optimal performance.
Conclusion
Dealing with a Generac generator 2800 error code can be frustrating but you’re not alone. By understanding the common causes and taking the right troubleshooting steps you can often resolve the issue quickly. Remember to keep an eye on fuel levels and maintain your generator regularly to prevent future problems.





If you find yourself stuck after trying the DIY fixes don’t hesitate to call in a professional. They can help you get your generator back in shape so you can have peace of mind during power outages. With a little effort you can keep your generator running smoothly and reliably when you need it most.
Frequently Asked Questions
What does Generac generator error code 2800 indicate?
The 2800 error code typically points to a fuel issue in the generator. This can include low fuel levels, clogged fuel filters, air in the fuel lines, or a faulty fuel pump, leading to concerns during a power outage.
How can I troubleshoot the 2800 error code?
Start by checking your fuel levels and inspecting for leaks. Clear any blockages in the fuel filter, bleed the fuel lines, and test the fuel pump. Don’t forget to examine electrical connections for any loose wires or battery problems.
What are common causes of the 2800 error code?
Common causes include low fuel levels, clogged fuel filters, air in fuel lines, faulty fuel pumps, and electrical problems like loose connections or faulty sensors. Neglecting maintenance, such as oil changes and filter replacements, can also contribute.
When should I seek professional help for a 2800 error?
If basic troubleshooting does not resolve the 2800 error code, or if you experience complicated electrical issues, it’s best to contact a licensed technician. They can diagnose and fix more complex problems to ensure safe and effective generator operation.
How can regular maintenance prevent the 2800 error code?
Regular maintenance—including oil changes, filter replacements, and routine inspections—helps keep the generator in good working condition. By running the generator monthly and maintaining its components, you can avoid fuel and electrical issues that lead to error codes.
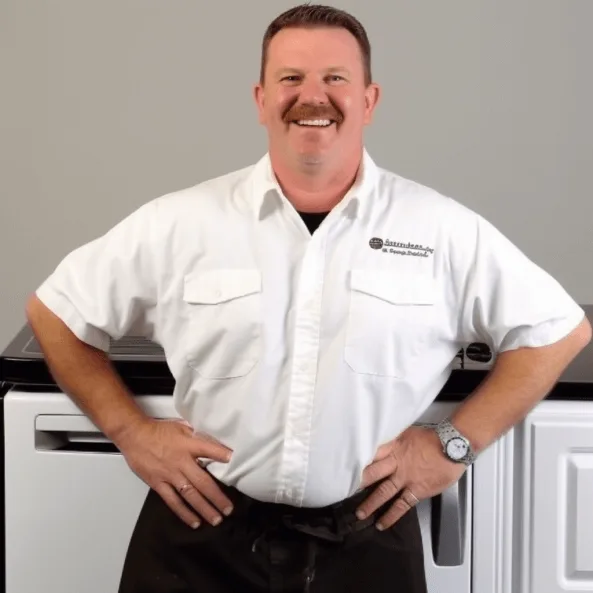
Hey, I’m Jake. I focus on cooling systems at Appliance Mastery, like fridges, freezers, and air conditioners.
I’ve worked in appliance repair for more than ten years and I’m certified through NASTeC. I’ve seen just about every fridge issue you can imagine.
My goal is to help you fix problems without stress. Whether it’s a freezer that won’t cool or an AC that keeps beeping, I’m here to walk you through it.