Have you ever found yourself in the middle of a power outage only to discover your generator’s fuel gauge isn’t working? You’re not alone. Many people face this frustrating issue, leaving them guessing how much fuel is left and whether their generator will keep running when they need it most.
In this article, you’ll learn about the common reasons your fuel gauge might fail and how to troubleshoot the problem. We’ll cover practical tips to help you get your gauge back in working order, ensuring you’re never left in the dark again. With a little guidance, you can regain control and have peace of mind when it comes to your generator’s fuel levels.
Key Takeaways
- Common Causes: Fuel gauge issues in generators often stem from electrical problems, sensor malfunctions, or dirt buildup affecting the sensor’s operation.
- Diagnosis Steps: Effective troubleshooting includes a thorough visual inspection of the gauge, wiring harness, and connections, followed by testing electrical connections using a multimeter.
- Repair and Replacement: For non-working gauges, consider repairing faulty connections or components, or replacing the gauge and sensor as needed to restore functionality.
- Preventive Maintenance: Regular maintenance practices, such as inspecting connections and cleaning sensors, can help prevent future fuel gauge malfunctions.
- Battery Health: Monitoring and maintaining battery condition is crucial, as a weak battery can impact the fuel gauge’s performance.
- Quality Fuel: Using high-quality fuel is important to avoid clogging sensors, ensuring accurate fuel level readings and overall generator efficiency.
Common Causes Of Generator Fuel Gauge Not Working
Understanding the common causes of a malfunctioning fuel gauge can help you troubleshoot the issue effectively. Here are key reasons why your generator’s fuel gauge may not be functioning properly.





Electrical Issues
Electrical problems often lead to fuel gauge malfunctions. Check for loose or corroded connections in the wiring harness. A faulty battery or blown fuse can also result in inaccurate readings. Inspect the electrical lines for signs of wear or damage. If you notice any issues, replacing damaged wiring or securing loose connections can solve the problem.
Sensor Malfunctions
Sensor failures frequently cause fuel gauge inaccuracies as well. The fuel level sensor could be dirty or stuck, affecting its ability to provide accurate readings. If your generator has a float sensor, ensure it moves freely within the tank. Clean the sensor if dirt buildup exists. Additionally, verify the sensor’s calibration; an uncalibrated sensor can lead to misleading gauge readings. Replacing a malfunctioning sensor restores accuracy.
How To Diagnose The Problem
Diagnosing a malfunctioning fuel gauge in your generator involves a few systematic steps. By focusing on visual inspections and testing electrical connections, you can pinpoint the issue effectively.
Visual Inspection
Start with a thorough visual inspection. Check the fuel gauge for obvious signs of damage or wear. Look for cracks, corrosion, or loose connections on the gauge itself. Inspect the wiring harness and connectors attached to the gauge. Ensure they are secure and free from dirt or debris. Pay attention to the fuel tank and its sensor; a blocked or contaminated sensor can lead to inaccurate readings. Cleaning the sensor and ensuring it moves freely often resolves gauge issues.
Testing Electrical Connections
Next, test the electrical connections. Gather a multimeter for this task. First, turn off the generator and disconnect the battery to avoid any accidental shorts. Set your multimeter to measure DC voltage. Reconnect the battery, and check the voltage at the gauge’s input. A functioning gauge requires a specific voltage; refer to your generator’s manual for exact values. If the readings fall outside the specified range, inspect the wiring for damage or poor connections. Additionally, test the ground connection; a loose or corroded ground can disrupt gauge operation. If everything checks out, but the gauge remains unresponsive, consider testing or replacing the gauge itself.





Solution Options
You can resolve a non-working fuel gauge through repair or component replacement. Here are the options you can explore:
Repairing The Fuel Gauge
Repairing your fuel gauge typically involves identifying and fixing specific issues. Start by examining the electrical connections. Look for loose wires or corroded terminals. Clean any corrosion using electrical contact cleaner.
After ensuring the connections are secure, check the gauge itself. If you find signs of damage, consider disassembling it for a closer look. Replace any burnt fuses or damaged components. If you’re comfortable with electronics, attempt to resolder connections for a more permanent fix.
Replacing Faulty Components
If the fuel gauge remains unresponsive, replacing faulty components may be necessary. Begin by locating replacement parts for your specific generator model. You’ll likely need a new gauge, sensor, or wiring harness.
To replace the gauge, disconnect the power source first. Remove the old gauge by unscrewing it from the panel. Install the new gauge by reversing the removal process and reconnect the wires carefully.





For sensor replacement, access the fuel tank. Detach the old sensor from its mount, then install the new sensor in the same position. Ensure a tight fit to prevent fuel leaks.
Regularly inspect and maintain your generator to minimize future fuel gauge issues.
Preventive Measures
Taking preventive measures helps maintain your generator’s fuel gauge functionality. Regular check-ups and proper care can reduce the risk of malfunctions.
Regular Maintenance Tips
- Inspect Connections: Regularly check for loose or corroded connections. Ensure wiring harnesses are secure and free from damage.
- Clean Sensors: Keep the fuel level sensors clean. Dirt buildup can cause inaccurate readings. Use a soft cloth for gentle cleaning.
- Check Battery Health: Monitor your battery condition. A weak or dying battery can affect gauge performance. Replace batteries as needed.
- Test the Gauge: Monthly, test the fuel gauge with a multimeter. Measure voltage at the gauge’s input. This helps identify electrical issues before they escalate.
- Fluid Levels: Regularly check fuel levels while the generator’s in use. Avoid running it on low fuel. This practice reduces strain on the gauge and helps prevent damage.
- Follow Manufacturer Guidelines: Always refer to the manufacturer’s manual for specific maintenance instructions. Each generator has unique requirements.
- Use Quality Fuel: Fill your generator with high-quality fuel. Poor-quality fuel can clog sensors, leading to malfunction.
- Store Properly: When not in use, store your generator in a dry, protected area. Weather exposure can cause corrosion or damage to components, including fuel gauges.
- Perform Periodic Inspections: Conduct visual inspections of the generator every few months. Check for any visible wear, signs of corrosion, or damage to components.
- Keep a Log: Maintain a maintenance log. Tracking inspections, repairs, and replacements helps you stay organized and identify patterns over time.
By following these preventive measures, you can ensure your generator’s fuel gauge remains reliable and functional.
Conclusion
Dealing with a malfunctioning fuel gauge can be frustrating but you’re not alone in this. By understanding the common causes and following the troubleshooting steps outlined, you can get your generator back on track. Remember to keep up with regular maintenance to prevent future issues.
Taking proactive measures now will save you from unexpected surprises later. Whether it’s cleaning sensors or checking connections, a little effort goes a long way in ensuring your generator runs smoothly. You’ll have peace of mind knowing you can monitor your fuel levels effectively, making your power outages a lot less stressful.
Frequently Asked Questions
What common causes lead to fuel gauge malfunctions in generators?
Fuel gauge malfunctions can often be attributed to electrical issues like loose or corroded connections, faulty batteries, or blown fuses. Additionally, dirty or stuck fuel level sensors can lead to inaccurate readings, making it essential to inspect and maintain these components regularly.
How can I diagnose a malfunctioning fuel gauge?
To diagnose a malfunctioning fuel gauge, begin with a visual inspection for damage or loose connections. Next, examine the wiring harness and fuel tank sensor for blockages. Use a multimeter to test DC voltage at the gauge’s input, verifying proper range and checking the ground connection.
What should I do if my fuel gauge is not working?
If your fuel gauge is not working, first check all electrical connections for damage or corrosion. Clean terminals and ensure the gauge itself is functional. If issues persist, consider replacing faulty components such as the gauge or sensor following manufacturer instructions for safe installation.
How can I prevent fuel gauge malfunctions in my generator?
To prevent fuel gauge malfunctions, conduct regular maintenance by inspecting connections for looseness or corrosion and cleaning sensors to avoid dirt buildup. Monitor battery health and perform monthly tests with a multimeter to catch electrical issues early. Regular visual inspections are also recommended.
Are there specific maintenance practices to ensure my fuel gauge works properly?
Yes, maintain your fuel gauge by following these practices: inspect and clean electrical connections, monitor battery health, and check for proper sensor movement. Regularly testing the gauge and keeping a maintenance log will help track its performance and catch potential issues early.
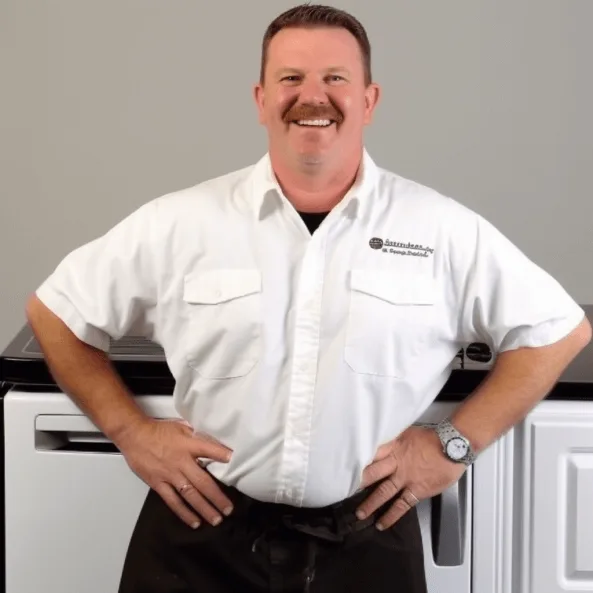
Hey, I’m Jake. I focus on cooling systems at Appliance Mastery, like fridges, freezers, and air conditioners.
I’ve worked in appliance repair for more than ten years and I’m certified through NASTeC. I’ve seen just about every fridge issue you can imagine.
My goal is to help you fix problems without stress. Whether it’s a freezer that won’t cool or an AC that keeps beeping, I’m here to walk you through it.