Ever wondered how to bring your AC compressor back to life without breaking the bank? Picture this: it’s a scorching summer day, and your AC suddenly stops working. Frustrating, right? But what if you could fix it yourself? In this article, you’ll discover the secrets to rebuilding your AC compressor like a pro.
Imagine the satisfaction of knowing you can tackle this common issue head-on, saving time and money in the process. By learning the ins and outs of rebuilding your AC compressor, you’ll be equipped to handle unexpected breakdowns with ease. Say goodbye to sweltering heat and hello to cool, comfortable living spaces – all thanks to your newfound skills.
Ready to take control of your AC’s fate? Get ready to dive into the world of AC compressor rebuilding and become your own cooling hero.
Understanding the AC Compressor
When it comes to your AC system, the compressor plays a crucial role in the cooling process. It’s like the heart of your air conditioner, pumping refrigerant to absorb and release heat, keeping your living spaces comfortable.
What Does the AC Compressor Do?
The AC compressor is responsible for pressurizing the refrigerant, turning it from a low-pressure gas to a high-pressure gas. This process is vital for the refrigerant to absorb heat from inside your home and release it outside.
Types of AC Compressors
There are two main types of AC compressors you may encounter:
- Piston Compressors: Common in older models, they work by compressing refrigerant with pistons.
- Scroll Compressors: Found in newer systems, they use spiral-shaped parts to compress the refrigerant efficiently.
Signs of Compressor Issues
Understanding the warning signs of a failing compressor can help prevent a complete breakdown. Look out for:
- Warm air blowing from vents when the AC is on.
- Unusual sounds like banging or rattling coming from the unit.
- Frequent cycling on and off, indicating compressor struggles.
Importance of Compressor Maintenance
Regular maintenance, such as cleaning coils and replacing filters, can extend your compressor’s lifespan. Ignoring maintenance can lead to costly repairs or premature compressor failure.
DIY Rebuilding: Is It for You?
Considering rebuilding your AC compressor can be a cost-effective way to address issues. With the right knowledge and tools, you can potentially save money and gain a deeper understanding of your AC system.
Remember, the more you know about your AC compressor, the better equipped you are to handle unexpected breakdowns and ensure your home stays cool and comfortable.
Signs of a Failing AC Compressor
A failing AC compressor shows specific symptoms that can help you identify issues early on. Here are some common signs to be aware of:
- Weak airflow: You might notice a decrease in airflow coming from your vents.
- Warm air: If the air blowing out isn’t as cool as it should be, your compressor could be struggling.
- Loud or strange noises: Unusual sounds like grinding, squealing, or clunking could indicate compressor problems.
- Leaking refrigerant: Puddles or noticeable leaks near the AC unit may point to compressor issues.
- Tripped circuit breaker: A failing compressor can cause electrical issues, leading to frequent circuit breaker trips.
Being attentive to these signs can help you address AC compressor problems promptly.
Gathering the Necessary Tools and Materials
When it comes to rebuilding your AC compressor, having the right tools and materials at hand is crucial for a successful project. Here’s what you need to get started:
- Safety glasses: Protect your eyes from any debris or oil during the process.
- Gloves: Ensure a firm grip and shield your hands from sharp edges.
- Ratchet and socket set: Essential for loosening and tightening bolts.
- New compressor kit: Includes seals, gaskets, and O-rings needed for replacement.
- Refrigerant recovery machine: To safely remove refrigerant from the system.
- AC manifold gauge set: Helps in checking pressure levels before and after the rebuild.
- Air compressor: Useful for cleaning components and blowing out debris.
- Torque wrench: Ensures proper tightening of bolts to manufacturer specifications.
- AC system flush kit: Cleans out the system before installing the rebuilt compressor.
Before diving in, make sure you have all these items handy. With the right tools and materials, you’ll be well-equipped to tackle the AC compressor rebuild with confidence.
Step-by-Step Guide to Rebuilding the AC Compressor
When rebuilding your AC compressor, it’s important to follow a systematic approach. Here’s a step-by-step guide to help you through the process:
- Step 1: Begin by safely disconnecting the battery to avoid any electrical mishaps during the repair.
- Step 2: Remove the old compressor carefully, ensuring you don’t damage any surrounding components.
- Step 3: Drain the compressor oil by tilting it and letting it sit for a few minutes.
- Step 4: Flush the AC system to remove any contaminants before installing the new compressor.
- Step 5: Install the new compressor kit following the manufacturer’s instructions.
- Step 6: Evacuate and recharge the AC system to ensure proper functioning of the compressor.
- Step 7: Check for leaks using an AC manifold gauge set to verify everything is sealed correctly.
Rebuilding your AC compressor requires attention to detail and following each step meticulously for optimal results.
Testing and Reinstalling the Rebuilt AC Compressor
Once you’ve rebuilt your AC compressor, it’s time to test it before reinstalling it in your vehicle. Here’s what you need to do:
- Testing the Rebuilt Compressor:
- Connect the compressor to a power source to ensure it engages smoothly.
- Use a multimeter to check electrical connectivity.
- Verify that the compressor runs quietly and without any unusual noises or vibrations.
- Reinstalling the Compressor:
- Follow the manufacturer’s instructions for proper installation.
- Ensure all connections are secure and properly sealed.
- Replace any O-rings to prevent leaks.
- Checking System Performance:
- Evacuate and recharge the AC system following recommended procedures.
- Monitor the system for proper cooling output.
- Final Checks:
- Inspect for any signs of leaking refrigerant.
- Check the system pressures and temperature differentials to confirm proper operation.
Remember, thorough testing and precise reinstallation are key to ensuring your rebuilt AC compressor performs optimally.
Conclusion
Ensuring proper testing and meticulous reinstallation are key to maximizing the efficiency of your rebuilt AC compressor. By following manufacturer guidelines, securing connections, and monitoring system performance, you can guarantee a successful outcome. Remember to pay attention to details such as O-ring replacements, system evacuations, and refrigerant recharges. Checking for leaks and verifying cooling output are essential steps in the process. Your commitment to thorough testing and precise reinstallation will result in a fully functional AC system that keeps you cool on the road.
Frequently Asked Questions
How important is testing a rebuilt AC compressor before reinstalling it?
Testing a rebuilt AC compressor before reinstalling it is crucial to ensure smooth engagement, proper functioning, and electrical connectivity for optimal performance in the vehicle.
What are the key steps involved in the reinstallation process of a rebuilt AC compressor?
The key steps include following manufacturer instructions, securing connections, replacing O-rings, evacuating and recharging the AC system, monitoring cooling output, checking for leaks, and confirming proper operation through system pressure and temperature checks.
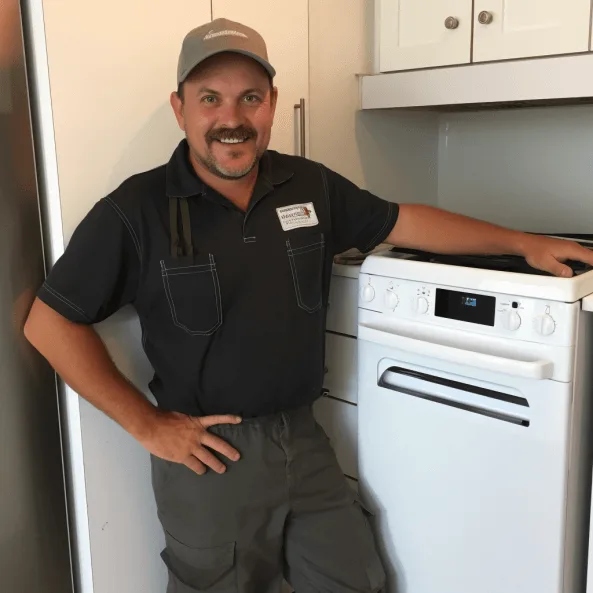
Hi, I’m Charlie, and I cover all things laundry here at Appliance Mastery.
I’ve spent over eight years working on washing machines, dryers, and dishwashers. I also have a degree in mechanical engineering, which helps me understand how these appliances really work.
I try to make every guide clear and practical. If you’re stuck with a noisy dryer or a leaking washer, I’ll help you figure out what’s wrong and how to fix it.