Have you ever reached for a refreshing drink only to find your bottom freezer’s ice maker isn’t working? It’s frustrating when you expect a chilled beverage and end up with an empty tray instead. You’re not alone—this is a common issue many people face.
Key Takeaways
- Common Causes: Mechanical issues like ice blockages, water supply line problems, and faulty components are primary reasons for an ice maker malfunction in bottom freezers.
- Electrical Issues: Problems with power supply, tripped circuit breakers, faulty wiring, and control module failures can prevent the ice maker from working properly.
- Troubleshooting Steps: Start with checking the power supply and water lines, ensuring the water valve is open and the filter is not clogged.
- Preventive Maintenance: Regular cleaning and maintaining optimal freezer temperatures between 0°F and 5°F help prevent ice maker issues and ensure efficient operation.
- Signs to Call a Professional: Indications like constant noise, leaking water, no ice production, or excessive frost may signal serious issues that require expert intervention.
- Cost Considerations: Repair costs can vary, so it’s essential to weigh them against the potential cost of replacing the ice maker, especially for older units.
Common Causes Of Ice Maker In Bottom Freezer Not Working
Identifying why your ice maker isn’t functioning can save time and frustration. Below are common culprits for this issue.
Mechanical Issues
Mechanical problems often cause ice makers to malfunction. Check these factors:
- Ice Blockage: Ice can form in the dispenser or mold, preventing new ice from being made. Remove any blockages to restore function.
- Water Supply Line: A kinked or frozen water line can impede water flow. Inspect the line for bends or ice buildup.
- Faulty Components: Parts like the ice maker assembly, motor, or water inlet valve may fail. Testing each component can pinpoint the issue.
- Temperature Settings: Ensure your freezer is set to 0°F. Inadequate cooling can interfere with ice production.
Electrical Problems
Electrical issues can also disrupt your ice maker’s operation. Check these elements:
- Power Supply: Ensure the ice maker is plugged in and that the outlet functions properly. Test it with another appliance if needed.
- Tripped Circuit Breaker: A tripped breaker can cut power to your ice maker. Locate the breaker panel and reset any tripped switches.
- Faulty Wiring: Damaged or corroded wires can limit power to the ice maker. Inspect the wiring for any visible issues.
- Control Module Failures: A malfunctioning control board can disrupt communication between components. If the board is faulty, consider replacement.
Investigating these mechanical and electrical issues often leads to finding the solution for an ice maker that isn’t working in your bottom freezer.
Troubleshooting Steps To Fix The Ice Maker
When your ice maker in a bottom freezer isn’t working, follow these troubleshooting steps to identify and address the issue.
Checking the Power Supply
Check the power supply to ensure the ice maker receives electricity. Inspect the power cord for any visible damage. If the cord appears fine, test the electrical outlet by plugging in another appliance. If the outlet has no power, reset the circuit breaker or replace the fuse. Confirm that the ice maker’s switch is turned on. If these steps show no issues, a professional may need to examine the wiring.
Inspecting Water Supply Lines
Inspect the water supply lines to ensure water flows to the ice maker. Start by checking the water supply valve behind the refrigerator. Ensure it’s fully open. Next, examine the water line for kinks or damage that may restrict flow. If necessary, disconnect the line and flush it to clear any blockages. If the water supply is connected and functioning, assess the water filter. A clogged filter can impede water flow, so replace it if it’s been six months or longer since the last change.
Preventive Maintenance Tips
Maintaining your ice maker prevents common issues and ensures consistent ice production. Follow these tips to keep your ice maker in top shape.
Regular Cleaning
Clean your ice maker every few months to prevent ice blockages and buildup. Remove ice from the bin and wash the interior with warm, soapy water. Rinse thoroughly to avoid soap residues. Also, clean the water supply components, ensuring no debris clogs the lines. For thorough cleaning, consider using a solution of vinegar and water to disinfect surfaces and prevent mildew. Regular cleaning keeps your ice maker functional and improves the taste of the ice.
Temperature Settings
Keep your freezer at the optimal temperature to ensure efficient ice production. The ideal temperature range for most freezers is between 0°F and 5°F (-18°C to -15°C). If your freezer is too warm, ice production slows down, and the ice maker may not work. Regularly check the freezer temperature using an appliance thermometer. Adjust the thermostat if needed, and allow 24 hours for the temperature to stabilize before checking again. Maintaining proper temperatures enhances your ice maker’s efficiency and longevity.
When To Call A Professional
If troubleshooting doesn’t restore your ice maker, consider reaching out to a professional. Certain signs may indicate more significant issues that require expert attention.
Signs of Major Issues
Look for these indicators to determine if professional help is necessary:
- Constant Noise: If your ice maker makes continuous grinding or unusual sounds, it might signal a malfunctioning component.
- Leaking Water: Puddles near the ice maker or water pooling in the freezer often point to a significant problem, such as a damaged water line.
- No Ice Production: If there’s no ice after following troubleshooting steps, a more serious issue could exist.
- Frost Buildup: Excessive frost around the ice maker or in the freezer can indicate airflow or defrosting problems.
Cost Considerations
Consider potential costs when deciding to call a professional. Here’s a breakdown of common expenses associated with ice maker repairs:
Service Type | Cost Range |
---|---|
Diagnostic Fee | $50 – $100 |
Component Replacement | $100 – $400 |
Labor Costs | $75 – $150 per hour |
Water Line Repair | $100 – $300 |
Before proceeding, ask for a detailed quote. Weigh the repair costs against the price of a new appliance, especially if your ice maker is older. Addressing issues promptly can save money in the long run and prevent further damage.
Conclusion
Dealing with a non-working ice maker can be a hassle but you’re not alone in this. By following the troubleshooting steps outlined and keeping up with preventive maintenance, you can often get your ice maker back on track. Remember to check those simple things first like the power supply and water lines.
If you still find yourself without ice after your efforts it might be time to call in a professional. Addressing these issues early can save you time and money down the road. Here’s to enjoying refreshing drinks with plenty of ice soon!
Frequently Asked Questions
Why is my bottom freezer ice maker not working?
The ice maker in your bottom freezer may not be working due to common issues such as ice blockages, water supply line problems, faulty components, or incorrect temperature settings. Check these areas to identify the root cause.
How can I troubleshoot my ice maker?
Begin by checking the power supply, including the power cord and outlet. Inspect the water supply lines for kinks or blockages. Additionally, ensure the freezer temperature is set correctly, ideally between 0°F and 5°F (-18°C to -15°C).
When should I call a professional for my ice maker?
Call a professional if troubleshooting doesn’t resolve the issue, especially if you notice constant noise, leaking water, lack of ice production, or excessive frost buildup, as these could indicate serious problems.
How often should I clean my ice maker?
It’s recommended to clean your ice maker every few months. Regular cleaning prevents ice blockages and buildup, ensuring efficient ice production and the longevity of the appliance.
What are the typical repair costs for an ice maker?
Repair costs can vary, but typically include diagnostic fees, parts replacement, and labor costs. Assess these expenses against the cost of a new appliance, particularly if your ice maker is older, to decide the best course of action.
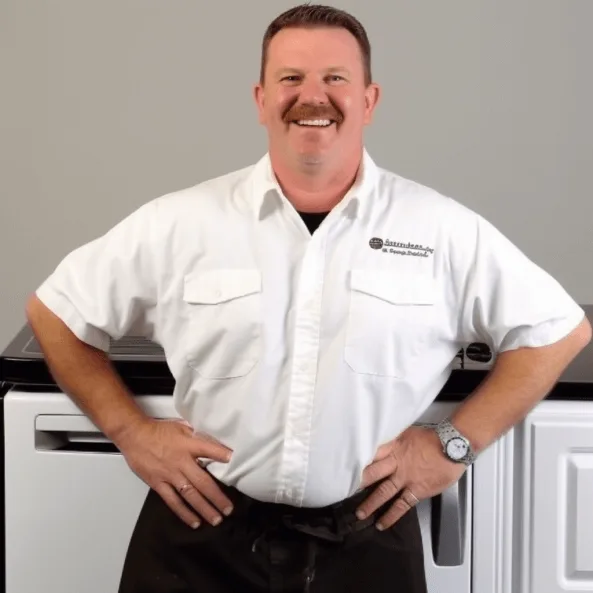
Hey, I’m Jake. I focus on cooling systems at Appliance Mastery, like fridges, freezers, and air conditioners.
I’ve worked in appliance repair for more than ten years and I’m certified through NASTeC. I’ve seen just about every fridge issue you can imagine.
My goal is to help you fix problems without stress. Whether it’s a freezer that won’t cool or an AC that keeps beeping, I’m here to walk you through it.