Has your Igloo deep freezer suddenly stopped working? You’re not alone. Many people face this frustrating issue, often right when they need it the most. Imagine opening that freezer to find your food thawed and spoiled—it’s a nightmare for anyone trying to keep groceries fresh.
In this article, you’ll learn the common reasons why your freezer might fail and how to troubleshoot the problem. We’ll share practical tips to help you get it back up and running, saving you time and money. Whether you’re a seasoned DIYer or a first-timer, you’ll find valuable insights to tackle this issue with confidence.
Key Takeaways
- Common Causes: Electrical issues, mechanical failures, and incorrect temperature settings are the primary reasons an Igloo deep freezer may stop working.
- Troubleshooting Steps: Simple checks, such as verifying the power supply, inspecting temperature controls, and ensuring proper airflow, can help diagnose freezer problems.
- Scheduled Maintenance: Regular cleaning of the interior and condenser coils, along with proper loading techniques, is essential for optimal freezer performance.
- Signs for Professional Help: Unusual noises, inconsistent temperatures, and visible physical damage are key indicators that a professional repair may be necessary.
- Choosing a Technician: Look for certified technicians with good reviews, request estimates, and ensure warranty coverage to protect your investment.
Common Causes For Igloo Deep Freezer Stopping
Understanding why your Igloo deep freezer stops working can help you troubleshoot the problem more effectively. Here’s a breakdown of the most common causes.





Electrical Issues
Electrical issues often lead to freezer failure. Check the following elements:
- Power Supply: Ensure your freezer is plugged in and the power outlet functions. Try plugging in another device to test the outlet.
- Fuses and Circuit Breakers: Inspect the fuses and circuit breakers. A blown fuse or tripped breaker can cut power to the unit.
- Extension Cords: If you use an extension cord, ensure it meets the freezer’s power requirements. Avoid using cords that can’t handle the load.
Mechanical Failures
Mechanical failures can affect the freezer’s performance. Key components to check include:
- Compressor: Listen for unusual noises. If the compressor runs constantly or not at all, it might need replacement.
- Condenser Coils: Dirty or blocked condenser coils can reduce efficiency. Clean the coils every six months to maintain optimal cooling.
- Fan Motors: Verify that fan motors operate correctly. If you don’t hear the fans running, they might require repairs or replacement.
Temperature Settings
Incorrect temperature settings can lead to food spoilage. Here’s how to fix it:
- Temperature Control: Ensure the temperature dial is set to the recommended setting, typically around 0°F (-18°C) for optimal freezing.
- Thermostat Malfunction: If the thermostat is faulty, it might not read the temperature accurately. Test the thermostat with a separate thermometer for verification.
- Frequent Door Opening: Limit the number of times you open the freezer door. Frequent access can cause temperature fluctuations that impact performance.
By addressing these common issues, you can restore your Igloo deep freezer to proper working order and keep your food safe.
Troubleshooting Steps
Follow these steps to diagnose and fix the issues with your Igloo deep freezer. Addressing the problem efficiently helps minimize the risk of food spoilage.





Checking Power Supply
- Verify Plug Connection: Ensure the freezer’s plug is securely connected to the outlet. A loose connection disrupts power supply.
- Inspect the Outlet: Test the electrical outlet with another device. If the device doesn’t work, the outlet might be faulty.
- Examine Extension Cords: If using an extension cord, check for any damage. Some cords can’t handle the power load of a freezer.
- Check for Tripped Circuit Breaker: Locate your circuit breaker box, and reset any tripped breakers. This can restore power easily.
- Inspect Fuses: Look for blown fuses and replace any that have burnt out, ensuring your freezer receives adequate power.
Examining Temperature Controls
- Adjust the Temperature Dial: Make sure the temperature setting is low enough. A higher setting may hinder cooling efficiency.
- Test the Thermostat: Check if the thermostat responds correctly. If it’s faulty, consider replacing it to stabilize temperature control.
- Limit Door Openings: Avoid frequently opening the freezer door. Each opening affects the internal temperature, compromising food preservation.
- Allow Adequate Space Around the Freezer: Ensure the freezer has sufficient airflow. Clean any dust or debris around vents and coils to enhance performance.
- Listen for Operation Sounds: Stand near the compressor and listen for humming sounds. If it’s silent, you may face an electrical or mechanical issue.
- Feel for Heat: Touch the compressor; it should feel warm but not overly hot. Excessive heat indicates an underlying problem.
- Clean the Condenser Coils: Dust or dirt on coils can impair cooling. Clean the coils with a soft brush or vacuum to improve efficiency.
- Check for Blockages: Ensure nothing obstructs the compressor fan. Proper airflow is crucial for maintaining the freezer’s functionality.
Maintenance Tips
Maintaining your Igloo deep freezer ensures it operates effectively and lasts longer. Follow these tips to keep your freezer in top shape.
Regular Cleaning
Keep the interior clean by wiping spills immediately and removing expired items regularly. Clean the condenser coils at least every six months to prevent dust buildup, which can hinder performance. Use a vacuum or a brush to remove dirt and debris. Also, ensure the door seal is free of dirt; a clean seal helps maintain temperature by preventing cold air from escaping.
Proper Loading Techniques
Avoid overloading your freezer. Overcrowding can restrict airflow, leading to uneven cooling. Store items in a way that allows air to circulate freely. Keep heavier items on the bottom and lighter ones on top. Leave space between items to enhance air circulation and ensure that cold air reaches all your food.
Routine Checks
Conduct routine checks on crucial components. Verify that the compressor runs without unusual noises, ensuring it functions smoothly. Check the temperature settings regularly; the ideal freezer temperature is 0°F (-18°C). Inspect the power cord and plug for wear or damage. If you notice any issues, address them promptly to prevent further problems. Listening for unusual sounds can also alert you to any mechanical issues before they escalate.
When To Call a Professional
If troubleshooting doesn’t resolve the issue with your Igloo deep freezer, calling a professional becomes essential. Prompt action can help prevent further damage and food spoilage.





Signs You Need Help
- Unusual Noises: If your freezer emits loud or strange noises, it may signal a mechanical problem.
- Inconsistent Temperature: Fluctuating temperatures can indicate a failing thermostat or compressor.
- Frequent Frost Buildup: Excessive frost or ice formation suggests a sealing issue or refrigerant leak.
- Increased Energy Bills: A sudden spike in energy costs often points to inefficient freezer operation.
- Physical Damage: Visible dents, cracks, or rust may compromise the appliance’s integrity and functionality.
- Look for Certifications: Select a technician with relevant certifications and experience in freezer repairs.
- Check Reviews: Read customer reviews to gauge their reliability and quality of service.
- Request Estimates: Obtain estimates from multiple services to compare costs and avoid overpaying.
- Ask About Warranty: Ensure that the repair includes a warranty for parts and labor, which protects your investment.
- Confirm Availability: Choose a service that can provide timely assistance, especially when food safety is at stake.
Conclusion
Dealing with an Igloo deep freezer that’s stopped working can be stressful but you’ve got the tools to tackle the issue. By understanding the common causes and following the troubleshooting steps, you can often restore your freezer to working order.
Remember that regular maintenance is key to preventing future problems. Keep an eye on the temperature settings and ensure proper airflow to keep your freezer running smoothly.
If you find yourself stuck despite your best efforts don’t hesitate to reach out for professional help. With a little patience and the right approach, you can keep your food safe and your freezer in great shape.
Frequently Asked Questions
What causes an Igloo deep freezer to stop working?
There are several common reasons for an Igloo deep freezer to stop working. These include electrical issues like power supply problems, blown fuses, or inadequate extension cords. Mechanical issues may also arise from problems with the compressor, condenser coils, or fan motors. Additionally, incorrect temperature settings or blockages can lead to operational failures.
How can I troubleshoot my Igloo deep freezer?
To troubleshoot your Igloo deep freezer, first check the plug connection and inspect the outlet for any issues. Verify that circuit breakers haven’t tripped and inspect fuses. Next, ensure the temperature dial is set correctly, test the thermostat, and limit door openings. Listening for operational sounds and checking for airflow are also crucial steps.
How often should I clean my Igloo deep freezer?
It’s recommended to clean your Igloo deep freezer at least every six months. Regular cleaning of the interior and condenser coils prevents dust buildup, which can affect performance. Additionally, ensuring the door seal is clean helps maintain the desired temperature inside the freezer.
When should I call a professional for freezer repair?
You should consider calling a professional if you notice unusual noises, inconsistent temperatures, frequent frost buildup, or visible physical damage. If troubleshooting does not resolve the issue, and you encounter high energy bills, a technician can diagnose and fix the problem effectively.
What maintenance tips can help extend the life of my deep freezer?
To extend the life of your deep freezer, regularly clean the interior and condenser coils, and ensure the door seal is intact and clean. Use proper loading techniques to avoid overcrowding, which can restrict airflow. Lastly, routinely check the compressor and temperature settings to catch any potential issues early.
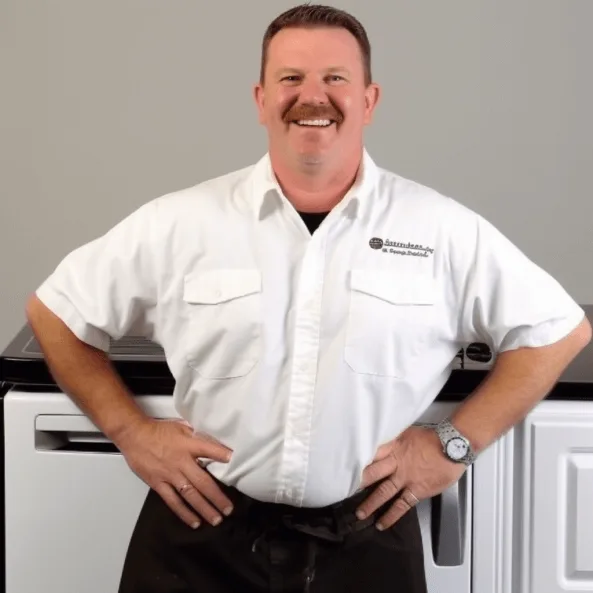
Hey, I’m Jake. I focus on cooling systems at Appliance Mastery, like fridges, freezers, and air conditioners.
I’ve worked in appliance repair for more than ten years and I’m certified through NASTeC. I’ve seen just about every fridge issue you can imagine.
My goal is to help you fix problems without stress. Whether it’s a freezer that won’t cool or an AC that keeps beeping, I’m here to walk you through it.