Have you ever opened your Kenmore bottom freezer only to find a puddle of water pooling beneath the ice maker? It’s a frustrating situation that can lead to bigger problems if not addressed quickly. You’re not alone—many people face this issue, and it often leaves you wondering what went wrong.
Key Takeaways
- Identify Common Issues: Understand that clogged drain lines, faulty water inlet valves, and damaged water supply lines are the primary causes of leaks in Kenmore bottom freezer ice makers.
- Regular Inspection: Regularly check the water supply line and ice maker assembly for damage, ice buildup, or blockages to prevent leaks and maintain functionality.
- Effective Troubleshooting: Follow detailed troubleshooting steps like inspecting the water supply line, examining the water inlet valve, and testing the ice maker’s operation to quickly resolve leaks.
- Preventive Maintenance: Implement routine maintenance practices, such as cleaning ice maker components and flushing drain lines, to minimize the risk of water leaks.
- Monitor Performance: Keep an eye on ice production rates and look out for signs of pooling water or unusual noises, which can indicate underlying problems with the ice maker.
- Immediate Action is Key: At the first sign of leaks or reduced ice production, inspect and address the issue promptly to avoid further damage to your appliance.
Overview of Kenmore Bottom Freezer Ice Makers
Kenmore bottom freezer ice makers provide convenient automatic ice production in many households. These appliances are designed to fit under standard kitchen counters, maximizing storage in both the refrigerator and freezer sections. While functional, they can develop issues, such as water leaks, which require your attention.
Common Features
- Ice Production Rate: Many models produce between 28 to 50 pounds of ice per day, meeting the needs of a family.
- Storage Capacity: Ice storage bins in these units typically hold 3 to 4 pounds of ice, ensuring a steady supply.
- Temperature Control: These ice makers maintain temperatures between 0°F and 5°F, preserving ice quality.
Working Mechanism
Kenmore bottom freezer ice makers use a water supply line connected to your home’s plumbing. When activated, they fill the ice mold with water, freeze it, and then eject the ice into the storage bin. The process recycles water efficiently, making it a reliable appliance for everyday use.





Potential Issues
Despite their reliability, these ice makers can experience leaks. Common causes of water pooling include:
- Clogged or Frozen Water Line: Ice obstructs the flow, resulting in leaks.
- Damaged Water Supply Line: Pinholes or cracks can develop, leading to water escape.
- Faulty Ice Maker Assembly: Wear and tear can impact seals and gaskets.
- Regular Maintenance: Inspect your water supply line for kinks or degradation.
- Keep the Freezer Clean: Ensure no ice buildup obstructs the water line.
- Monitor for Leaks: Regularly check beneath the ice maker for signs of pooling water.
By understanding the features and common issues of Kenmore bottom freezer ice makers, you equip yourself to tackle potential concerns effectively.
Common Causes of Leaking Water
Understanding the reasons behind your Kenmore bottom freezer ice maker leaking water can help you fix the issue swiftly. Here are the most common causes:
Clogged Drain Lines
Clogged drain lines often lead to water pooling under the ice maker. Ice makers typically have a drain system that carries excess water away. If this drain line gets clogged with debris or ice, it can cause water to back up, resulting in leaks.
- Check for Blockages: Inspect the drain line for any visible blockages, such as ice buildup or food particles.
- Clear the Drain: Use a pipe cleaner or a similar tool to remove any obstruction. If necessary, warm water can help melt ice blockages.
Faulty Water Inlet Valve
A faulty water inlet valve can also cause leaks. This valve controls the flow of water into your ice maker. If it fails, it may allow water to continuously flow, leading to leaking.





- Inspect the Valve: Look for signs of wear or damage on the valve. A visual check can reveal cracks or corrosion.
- Test the Valve: You can test the valve with a multimeter for continuity. Replace it if the reading indicates it’s faulty.
- Replace as Needed: Purchase a compatible water inlet valve and follow the manufacturer’s instructions for installation.
By identifying these common causes, you can take appropriate action to fix the leaking ice maker and maintain its functionality.
Troubleshooting Steps
Follow these troubleshooting steps to address a leaking ice maker in your Kenmore bottom freezer. You’ll identify and resolve common issues effectively.
Inspecting the Water Supply Line
- Locate the water supply line at the back of your refrigerator. Check for any visible damage, including kinks, cuts, or cracks. These can lead to leaks.
- Disconnect the water supply line from the refrigerator. Use a towel to catch any water that spills during disconnection. Inspect the connection point for blockages or wear.
- Flush the line by running water through it. This helps clear any debris that might cause a blockage.
- Reconnect the line securely. Make sure the connection is tight but avoid over-tightening, as this could damage the fitting.
- Access the ice maker assembly. This typically involves removing the cover of the ice maker.
- Examine the water inlet valve for signs of wear or leaks. If the valve is faulty, it may continuously supply water, leading to pooling.
- Inspect the ice mold for ice buildup. Ice can obstruct water flow and cause leaks. If frost is present, you may need to defrost the ice maker.
- Manipulate the ice maker’s arm (if applicable) to check if it moves freely. A stuck arm can prevent proper operation and may result in leaks.
- Test the ice maker by cycling it through a complete operation. Observe if any leaks occur during production.
Implementing these steps can resolve most common issues with your Kenmore bottom freezer ice maker. Regular inspections and maintenance ensure reliable performance and minimize the risk of leaks.
Preventive Measures
Taking preventive measures can help you avoid issues with your Kenmore bottom freezer ice maker leaking water. Regular maintenance and vigilant monitoring keep your appliance running smoothly.
Regular Maintenance Tips
- Inspect Water Supply Line: Check for any visible damage, kinks, or leaks. Tighten connections to prevent water escape.
- Clean Ice Maker Components: Regularly remove ice buildup in the ice mold to ensure proper operation. Use warm water to melt excess ice safely.
- Flush Drain Lines: Periodically run warm water through your drain lines to prevent clogs. Clear out any debris you find.
- Check Water Inlet Valve: Inspect the valve for wear or blockages. If the valve is stuck open, it’ll cause leaks.
- Monitor for Changes: Keep an eye on ice production rates. A sudden drop may indicate underlying problems.
- Puddles Under Ice Maker: If you notice water pooling, it’s a clear sign of a leak. Immediate inspection is necessary.
- Reduced Ice Production: A decrease in the amount of ice produced may indicate a clog or malfunction that requires attention.
- Frost Build-Up: Excessive frost in the ice maker can signal drainage issues or a blocked air vent.
- Unusual Noises: If you hear loud or strange noises from your ice maker, it might suggest mechanical problems needing an expert’s evaluation.
- Ice Smell or Taste: Foul odors or tastes in ice can indicate food contamination or a dirty ice maker that requires cleaning.
These preventive measures and attentiveness to signs of potential issues can help you maintain your Kenmore bottom freezer ice maker and prevent water leaks.





Conclusion
Dealing with a leaking ice maker can be frustrating but you’re not alone in this. By understanding the potential causes and taking proactive steps, you can keep your Kenmore bottom freezer running smoothly. Regular maintenance and vigilance are key to preventing leaks and ensuring your ice maker operates efficiently.
Remember to inspect the water supply line and clean the components regularly. Keeping an eye out for signs of trouble can save you time and hassle down the road. With a little attention and care, you can enjoy hassle-free ice production for years to come.
Frequently Asked Questions
What causes water to pool beneath my Kenmore bottom freezer ice maker?
Water pooling can occur due to clogged or frozen water lines, damaged supply lines, or a faulty ice maker assembly. Regular inspection and maintenance can help prevent these issues.
How much ice does a Kenmore bottom freezer ice maker produce?
Kenmore bottom freezer ice makers can produce between 28 to 50 pounds of ice per day and hold 3 to 4 pounds in storage. This allows for ample supply for daily use.
What maintenance can I perform to prevent leaks?
To prevent leaks, regularly inspect the water supply line for damage, clean components to avoid ice buildup, flush drain lines to prevent clogs, and check the water inlet valve for wear.
How do I troubleshoot my ice maker if it’s leaking?
Start by inspecting the water supply line for damage and flushing it to clear any blockages. Also, check the ice maker assembly, water inlet valve, and ice mold for any signs of wear or ice buildup.
What should I do if my water inlet valve is faulty?
If the water inlet valve is worn or damaged, it should be tested and replaced if necessary. Ensure secure connections and proper functioning to stop continuous water flow that may cause leaks.
How can I tell if my ice maker needs repair?
Look for signs like puddles under the ice maker, reduced ice production, frost build-up, unusual noises, or strange smells and tastes in the ice. These can indicate underlying issues that need addressing.
Is regular monitoring really necessary for ice makers?
Yes, regular monitoring is crucial in spotting potential problems early. Keeping an eye on ice production, water pooling, and other signs can prevent further complications and costly repairs.
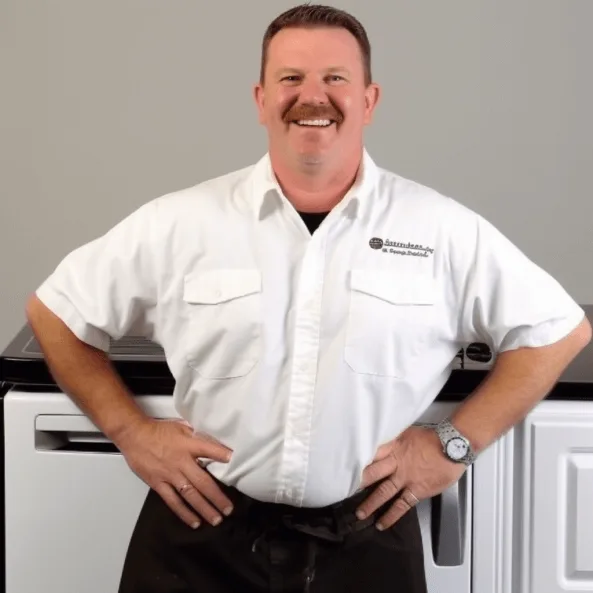
Hey, I’m Jake. I focus on cooling systems at Appliance Mastery, like fridges, freezers, and air conditioners.
I’ve worked in appliance repair for more than ten years and I’m certified through NASTeC. I’ve seen just about every fridge issue you can imagine.
My goal is to help you fix problems without stress. Whether it’s a freezer that won’t cool or an AC that keeps beeping, I’m here to walk you through it.