Have you ever found yourself in the middle of a power outage, only to discover your Ryobi 2300 generator screen isn’t working? It’s frustrating when you rely on your generator for backup power, and the screen goes blank just when you need it most.
You’re not alone in facing this issue. Many users encounter similar problems, and it can leave you feeling stuck and unsure of what to do next. This article will guide you through common reasons why your generator screen might not be functioning and offer practical solutions to get it back up and running. With a little troubleshooting, you can regain control and ensure your generator is ready when you need it.
Key Takeaways
- Common Screen Issues: The Ryobi 2300 generator screen may not work due to power supply issues, loose connections, or a faulty display unit. Identifying these causes is crucial for effective troubleshooting.
- Regular Maintenance: Performing routine checks on oil levels, air filters, and fuel quality enhances generator performance and reduces the likelihood of screen malfunctions.
- Troubleshooting Steps: Start by checking the power supply, ensuring adequate fuel and oil levels, and inspecting connections to diagnose and resolve screen issues effectively.
- DIY Repair Options: Simple solutions like cleaning contacts, re-seating connections, or performing a reset can often restore screen functionality without professional help.
- Professional Assistance: If troubleshooting fails, consider contacting a professional, especially if internal damage or warranty considerations are involved, to ensure safe and proper repair.
Overview of Ryobi 2300 Generator
The Ryobi 2300 generator serves as a compact, portable power source suitable for various applications. It supplies 2300 starting watts and 1800 running watts, providing sufficient power for recreational activities, home use, or emergencies.





Key features enhance its usability:
- Inverter Technology: This technology produces clean power for sensitive electronics, such as laptops and smartphones.
- Lightweight Design: Weighing around 53 pounds, it’s easy to transport and maneuver.
- Runtime: With a 1.2-gallon tank, the generator offers up to 8 hours of runtime at 25% load, ensuring prolonged operation during outages.
- Control Panel: It includes multiple outlets, ensuring compatibility with various devices.
Regular maintenance improves performance and extends the generator’s lifespan. Checking the oil level and air filters, along with cleaning the fuel system, prevents common issues.
Understanding these aspects ensures you maximize the efficiency and reliability of your Ryobi 2300 generator, providing peace of mind during power interruptions.
Common Issues with Ryobi 2300 Generator
The Ryobi 2300 generator can encounter several issues, with a malfunctioning screen being one of the most common frustrations. Recognizing these problems helps ensure efficient troubleshooting and maintenance.
Screen Malfunction
A malfunctioning screen on your Ryobi 2300 generator can stem from various causes. Here are a few potential reasons:





- Power Supply Issues: If the generator’s power isn’t stable, the screen may not function. Check the power output and ensure your generator is generating enough electricity.
- Loose Connections: Inspect the wiring connected to the screen. Loose or damaged wires can prevent the display from receiving power.
- Faulty Display Unit: A defective screen itself can lead to failure. Consider consulting a professional for a replacement if all other checks don’t resolve the issue.
Other Possible Issues
Besides a malfunctioning screen, other problems can occur with the generator. Here are key issues to monitor:
- Overloading: Using too many devices can overload the generator, potentially causing it to shut down. Ensure total wattage of connected devices does not exceed 2300 starting watts or 1800 running watts.
- Fuel Quality: Poor-quality fuel can result in starting or running issues. Always use clean, fresh gasoline to ensure optimal performance.
- Oil Level: Regularly check oil levels. Low oil can trigger the engine shutdown feature, halting operations abruptly.
- Air Filter Condition: A clogged air filter can reduce airflow, resulting in performance issues. Clean or replace the air filter regularly.
By regularly checking these components and addressing issues promptly, you can maintain your Ryobi 2300 generator in excellent working condition.
Troubleshooting Steps for Screen Issues
Screen issues on your Ryobi 2300 generator can often be resolved with some straightforward troubleshooting. Follow these steps to diagnose and correct the problem.
Checking Power Supply
- Verify that the generator is turned on. If it’s not, the display won’t activate.
- Ensure the fuel tank contains an adequate amount of fuel. Insufficient fuel can prevent the generator from operating properly.
- Check the oil level. Low oil levels may trigger a shutdown, causing the screen to go dark.
- Confirm the generator is connected to a compatible electrical load. An incompatible load could cause the generator to shut down.
- Monitor the battery condition. A dead or weak battery can affect the display’s functionality.
- Inspect the connections to the display unit. Loose or corroded wires can hinder the screen’s operation.
- Examine connections for signs of wear or damage. Frayed wires may cause intermittent issues or complete failure of the display.
- Re-seat all plugs to ensure they’re connected securely. Sometimes, simply ensuring a tight connection can resolve the problem.
- Check the connection to the generator’s main control board. A loose connector here can impact the screen’s performance.
- Review the user manual for proper connection diagrams. Following these instructions can help you avoid potential pitfalls.
Repair or Replacement Options
When facing a malfunctioning screen on your Ryobi 2300 generator, you have options for repair or replacement. Assess the situation carefully to determine the best course of action.
DIY Repair Tips
- Check the Power Source: Ensure the generator is plugged in and that the power supply is functioning. Test with another device if unsure.
- Inspect Connections: Look for loose or damaged connections between the display unit and the generator. Re-seat any connections to ensure they’re secure.
- Clean Contacts: Dust or corrosion on the terminals can disrupt the display. Clean the contacts gently with rubbing alcohol and a cotton swab.
- Reset the Generator: Turn off the generator for a few minutes before turning it back on. This simple reset can often resolve minor issues.
- Update Firmware: If your model supports it, check for any available firmware updates on the Ryobi website that may address screen functionality.
- Persistent Issues: If the screen remains non-functional despite troubleshooting, it’s time to consult a professional.
- Internal Damage: If you suspect damage to internal components, don’t open the unit yourself. Seek expert assistance for safety and compliance.
- Warranty Considerations: If your generator is still under warranty, contact Ryobi service. Professional repairs might be covered, saving you costs.
- Complex Repairs: When the problem requires specialized tools or knowledge, hiring a technician ensures proper repair and maintains safety standards.
Conclusion
Taking care of your Ryobi 2300 generator means being proactive about potential issues like a malfunctioning screen. By following the troubleshooting steps and maintaining your generator regularly you can keep it running smoothly when you need it most. Don’t forget to check connections and ensure you’re using quality fuel to avoid common pitfalls.





If problems persist consider reaching out to a professional for help. Keeping your generator in top shape not only enhances its performance but also gives you peace of mind during power outages. With a little attention you can ensure your generator serves you reliably for years to come.
Frequently Asked Questions
What should I do if my Ryobi 2300 generator screen is not working?
First, check the power supply to ensure the generator is turned on and has fuel and oil. Inspect connections to the display unit for any damage. If the issues continue, try resetting the generator or consulting the user manual for further guidance.
What causes a Ryobi 2300 generator screen to malfunction?
Common causes include power supply issues, loose or damaged connections, a faulty display unit, and operator error, such as overload or using poor-quality fuel. Regular maintenance can help prevent these problems.
How can I troubleshoot a malfunctioning screen on my Ryobi generator?
To troubleshoot, check the power supply, ensure the generator is on, verify fuel and oil levels, and inspect connections. Clean contacts and reseat plugs as necessary. If the problem persists, consult a professional technician.
Can I repair the Ryobi 2300 generator screen myself?
Yes, you can attempt DIY repairs by checking power sources, inspecting and cleaning connections, and resetting the generator. However, if you suspect internal damage or if the issue continues, seek help from a qualified technician.
What maintenance should I perform on my Ryobi 2300 generator?
Regular maintenance includes checking and changing the oil, cleaning the fuel system, inspecting the air filter, and monitoring electrical connections. Consistent upkeep maximizes efficiency and longevity during power outages.
When should I contact a professional for generator repairs?
Contact a professional if you suspect complex internal damage, if the generator is under warranty, or if you feel uncomfortable performing repairs. Professional assistance ensures safety and adherence to repair standards.
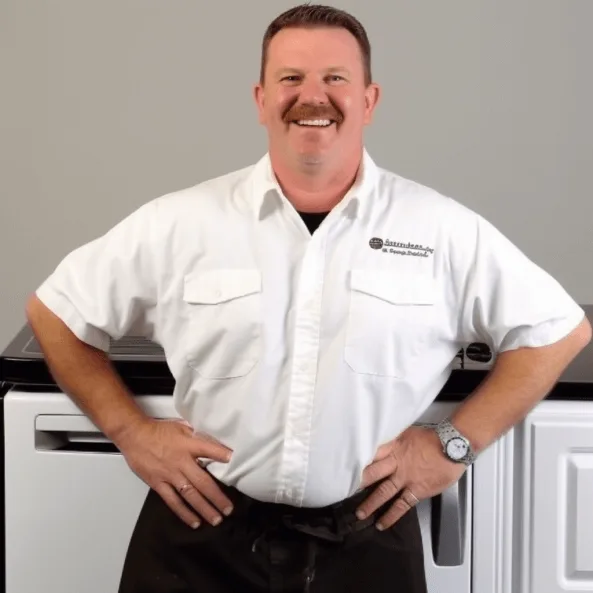
Hey, I’m Jake. I focus on cooling systems at Appliance Mastery, like fridges, freezers, and air conditioners.
I’ve worked in appliance repair for more than ten years and I’m certified through NASTeC. I’ve seen just about every fridge issue you can imagine.
My goal is to help you fix problems without stress. Whether it’s a freezer that won’t cool or an AC that keeps beeping, I’m here to walk you through it.