Have you ever noticed water pooling around your heating system? A leaking secondary heat exchanger could be the culprit. This common issue can lead to bigger problems if left unchecked, affecting not just your comfort but also your wallet.
Key Takeaways
- Importance of Secondary Heat Exchangers: These components are essential for efficient heat transfer in heating systems, ensuring temperature regulation and energy conservation.
- Signs of a Leak: Look for visible water pooling, reduced efficiency, and unusual noises like banging or gurgling, which may indicate a secondary heat exchanger leak.
- Common Causes: Leaks can result from corrosion, improper installation, or system overpressure; regular maintenance is essential to mitigate these risks.
- Diagnostic Methods: Conduct visual inspections and pressure testing to effectively locate leaks and prevent further damage to the heating system.
- Repair vs. Replacement: Small leaks may be resolved with sealing solutions, while significant damage may require complete unit replacement for long-term efficiency and reliability.
- Maintenance Tips: Regularly inspect the system, clean sediment buildup, and monitor pressure levels to avoid leaks and ensure optimal performance.
Overview of Secondary Heat Exchangers
Secondary heat exchangers play a crucial role in heating systems, transferring heat from one fluid to another without mixing them. These devices often serve in high-efficiency heating units and can be found in various applications, including boilers and water heaters.
Functions of Secondary Heat Exchangers
- Heat Transfer: They efficiently transfer heat from the primary heating source to the secondary loop, often enhancing overall system efficiency.
- Temperature Regulation: By managing the temperature of the output fluid, they ensure a consistent heating supply for your home.
- Energy Conservation: Secondary heat exchangers help reduce operating costs by maximizing thermal efficiency.
Common Types
- Finned Tube Exchangers: These feature fins that increase surface area, improving heat transfer rates.
- Plate Heat Exchangers: Known for compact designs, these exchangers stack multiple plates for effective heat exchange.
- Shell and Tube Exchangers: Featuring tubes within a shell, they provide versatility in various industrial applications.
Signs of Problems
Be alert to these indicators of a leaking secondary heat exchanger:





- Visible Water Pooling: Moisture accumulating around the unit often signals a leak.
- Reduced Efficiency: If your heating system struggles to maintain temperature, it might relate to a malfunctioning heat exchanger.
- Unusual Noises: Banging or gurgling sounds can indicate air trapped in the system, often a result of water leaks.
Maintenance Tips
- Regular Inspections: Check the unit for signs of wear or corrosion at least once a year.
- Clean the System: Remove sediment buildup to ensure efficient operation.
- Monitor Pressure Levels: Regularly check system pressure; an unexpected drop can indicate leaks.
- Identify Leak Location: Use a flashlight to inspect joints and seams; look for moisture or corrosion.
- Check System Connections: Ensure that all hoses and fittings are tight and intact.
- Consult Professionals: If DIY solutions don’t resolve issues, contact a heating specialist for repairs.
By understanding the role and maintenance of secondary heat exchangers, you can help prevent potential leaks, ensuring your heating system operates efficiently.
Common Causes of Secondary Heat Exchanger Leaking Water
Secondary heat exchangers can leak water for several reasons. Identifying these causes helps you address issues promptly and maintain your heating system’s efficiency.
Corrosion and Wear
Corrosion often leads to leaks in secondary heat exchangers. Factors such as water quality, temperature fluctuations, and the materials used can accelerate corrosion. Over time, wear and tear can weaken the exchanger’s structure, creating small holes. Regularly checking for rust or scaling can help you catch these issues early. Implementing proper water treatment can also reduce corrosion risk.
Improper Installation
Improper installation can contribute to leaks in secondary heat exchangers. Issues such as incorrect alignment, inadequate sealing, or poorly fitted connections can create stress points. These stress points may become weak spots over time. To prevent this, ensure your heat exchanger is installed according to manufacturer guidelines. Hiring a qualified technician can help you avoid installation errors.
System Overpressure
System overpressure is another common cause of leaks in secondary heat exchangers. Elevated pressure can result from closed valves, malfunctioning pressure relief valves, or excessive heat. When pressure exceeds the exchanger’s tolerance, it can cause seams to fail or joints to separate. Monitoring system pressure regularly and adjusting settings can help you maintain optimal levels, preventing leaks from occurring.





Symptoms of a Leaking Secondary Heat Exchanger
Identifying a leaking secondary heat exchanger early helps prevent further damage and higher repair costs. Here are key symptoms to watch for:
Unusual Sounds
Listen for strange noises coming from your heating system. These sounds may include:
- Banging or clanging: This can indicate water movement issues or loose components.
- Hissing sounds: A sign of steam or water escaping from a leak.
- Gurgling: Often results from air trapped in the system due to a leak.
Promptly addressing these sounds can prevent more extensive damage.
Increased Water Usage
Monitor your water bills for unusual spikes. A leak in the secondary heat exchanger typically leads to:
- Rising water consumption: An increase in your water usage without changes in routine may indicate a leak.
- Frequent refilling of the system: If you’re often adding water to your heating system, it’s time to investigate.
Regularly check for these signs to ensure the efficiency of your heating system and avoid costly repairs.





Diagnostic Methods for Leak Detection
Detecting leaks in a secondary heat exchanger is crucial for preventing further damage. Several methods exist for identifying leaks effectively.
Visual Inspections
Conduct visual inspections regularly. Look for obvious signs, such as water pooling around the unit or corrosion on the surface. Check for cracks, rust, or mineral deposits that may indicate leaks. Inspect connections, joints, and fittings closely, as these areas are common leak points. Perform these inspections after heating cycles, allowing time for condensation to accumulate, making leaks more visible.
Pressure Testing
Pressure testing helps locate leaks not visible to the naked eye. First, isolate the heat exchanger from the system and reduce pressure to zero. Next, introduce air into the exchanger to a specified pressure level, usually between 5-10 psi, depending on the system design. Monitor the pressure gauge for any drops over time. A decreasing pressure reading suggests a leak. For accurate results, use a soap solution on joints and connections; bubbles will form if there’s a leak.
Repair and Replacement Options
Addressing a leaking secondary heat exchanger requires careful consideration of repair and replacement options. You can choose between sealing solutions or complete unit replacement, depending on the severity of the leak and overall system condition.
Sealing Solutions
When leaks are small, sealing solutions can effectively address the problem. You can apply sealant compounds specifically designed for heat exchangers, targeting joints and cracks. Here’s a step-by-step approach to using sealing solutions:
- Identify the Leak: Use the diagnostic methods discussed earlier to locate the exact point of the leak.
- Drain the System: Turn off the heating system, and drain the water from the heat exchanger to ensure safety and ease of application.
- Prepare the Surface: Clean the area around the leak, removing any debris or moisture to allow a better bond.
- Apply Sealant: Follow the manufacturer’s instructions to apply the sealant. Ensure you cover the entire leak area thoroughly.
- Allow to Cure: Let the sealant cure as per the guidelines before refilling the system with water.
Sealing solutions can provide a quick fix for minor leaks, helping you avoid costly repairs if the leakage isn’t severe.
Complete Unit Replacement
If the leak is significant or if the secondary heat exchanger shows signs of extensive corrosion or wear, complete unit replacement might be necessary. Here’s how to approach the replacement:
- Assess the Damage: Evaluate the overall condition of the heat exchanger. If it’s rusted or has multiple leaks, replacement is more efficient.
- Choose the Right Unit: Select a replacement heat exchanger that matches your existing system’s specifications. Consult with a professional if you’re unsure.
- Shut Down the System: Turn off the heating system and isolate the damaged heat exchanger.
- Remove the Old Exchanger: Disconnect the water and any electrical connections, then carefully remove the old unit.
- Install the New Exchanger: Position the new unit, reattach connections, and ensure all fittings are tight and secure.
- Test the System: Refill the system with water, restore power, and monitor for leaks.
Complete replacement typically offers a long-term solution, providing you with better efficiency and reliability in your heating system.
Conclusion
Addressing a leaking secondary heat exchanger promptly can save you from costly repairs and ensure your heating system runs smoothly. By staying vigilant for signs like water pooling and unusual sounds you can catch issues early. Regular maintenance and inspections are key to prolonging the life of your system and maintaining efficiency.
If you suspect a leak don’t hesitate to take action. Whether it’s a minor fix or a complete replacement understanding the problem will help you make informed decisions. Keeping your heating system in top shape not only boosts comfort but also keeps your energy bills in check. Stay proactive and enjoy a warm and worry-free home.
Frequently Asked Questions
What causes water pooling around heating systems?
Water pooling around heating systems is often caused by a leaking secondary heat exchanger. This can be due to corrosion, improper installation, or system overpressure. If not addressed promptly, it can lead to larger issues and increased costs.
How can I detect a leak in my heating system?
Look for visible signs such as water pooling, unusual noises like banging or gurgling, and monitor water bills for spikes. Regular visual inspections and checking connections after heating cycles can help spot leaks early.
What are the symptoms of a leaking secondary heat exchanger?
Key symptoms include visible water pooling, reduced system efficiency, unusual noises like hissing or gurgling, and increased water bills. Noticing these signs early can help prevent further damage and higher repair costs.
How can I maintain my secondary heat exchanger?
Regular maintenance includes conducting inspections, cleaning the unit, monitoring pressure levels, and keeping track of any unusual sounds. Being proactive about maintenance can extend the life of the heating system and reduce the risk of leaks.
What repair options are available for a leaking secondary heat exchanger?
For minor leaks, sealing solutions can be applied. For significant issues, complete replacement of the heat exchanger may be necessary. It’s essential to properly assess the damage and follow installation procedures for replacements.
How does the secondary heat exchanger work?
The secondary heat exchanger transfers heat between fluids without mixing them. It plays a crucial role in temperature regulation and energy conservation within the heating system, ensuring efficient operation.
What types of secondary heat exchangers are common?
Common types include finned tube, plate, and shell and tube heat exchangers. Each type has unique designs and applications, suited for different heating system needs.
Why is early detection of a leak important?
Early detection of a leak is crucial to prevent more serious damage and costly repairs. Addressing the issue promptly can help maintain system efficiency and ensure comfort within your space.
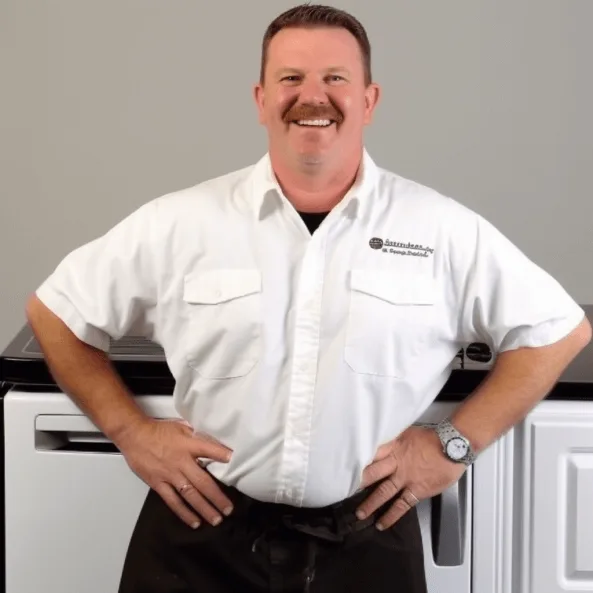
Hey, I’m Jake. I focus on cooling systems at Appliance Mastery, like fridges, freezers, and air conditioners.
I’ve worked in appliance repair for more than ten years and I’m certified through NASTeC. I’ve seen just about every fridge issue you can imagine.
My goal is to help you fix problems without stress. Whether it’s a freezer that won’t cool or an AC that keeps beeping, I’m here to walk you through it.