Is your Sub Zero 632 freezer refusing to keep things frozen? You’re not alone. Many people face this frustrating issue, and it can throw a wrench in your meal prep and food storage plans.
In this article, you’ll find practical tips to troubleshoot your freezer and get it back to its optimal performance. Whether it’s a minor glitch or a more serious problem, understanding the common causes can save you time and money. Let’s help you regain control over your kitchen and ensure your food stays fresh.
Key Takeaways
- Common Issues: Recognize that damaged door seals, blocked vents, and dirty condenser coils are frequent causes of Sub Zero 632 freezer malfunctions.
- Troubleshooting Steps: Efficiently diagnose issues by checking the power supply, inspecting door seals, and evaluating temperature control settings.
- Temperature Settings: Ensure the freezer’s temperature is set between -5°F and 0°F for optimal food preservation.
- When to Seek Professional Help: Persistent temperature issues, unusual noises, visible damage, or electrical problems may require expert assistance.
- Maintenance Tips: Regular cleaning of door seals, air vents, and condenser coils can enhance performance and longevity of the freezer.
- Age Consideration: If your freezer is over ten years old and consistently problematic, it may be time for a professional evaluation to avoid costly repairs.
Overview Of Sub Zero 632 Freezer
The Sub Zero 632 freezer integrates advanced technology for optimal food preservation. Understanding its components can help troubleshoot issues effectively.





Features
- Dual Refrigeration System: This system separates the freezer and fridge. It maintains ideal humidity levels, enhancing preservation.
- Temperature Control: The precise temperature settings allow adjustments down to 0°F. This feature supports various storage needs.
- Airflow Design: The unit’s innovative airflow design promotes even cooling, preventing temperature fluctuations.
Common Issues
Several factors can lead to the Sub Zero 632 freezer not functioning properly:
- Door Seals: Damaged or dirty seals can cause air leaks. Regular cleaning ensures efficiency.
- Vent Blockages: Obstructions in airflow can hinder cooling. Keep vents clear for optimal performance.
- Condenser Coils: Dirty condenser coils reduce efficiency. Cleaning these coils every six months enhances cooling.
Troubleshooting Tips
When the freezer stops working, you can take the following steps:
- Examine Door Seals: Check for any gaps or tears. Replace or clean as necessary to ensure proper sealing.
- Clear Air Vents: Inspect for any items blocking airflow. Remove any obstructions to restore proper circulation.
- Clean Condenser Coils: Turn off the unit, then gently brush away dust and debris from the coils.
- Adjust Temperature Settings: Verify the temperature setting is correct. Recalibrate the thermostat if needed.
- Monitor Loud Noises: Listen for unusual sounds, which can indicate mechanical issues. If these persist, professional help may be necessary.
The Sub Zero 632 freezer offers reliable performance and longevity when maintained properly. Understanding its features and operating protocols ensures consistent, optimal functionality.
Common Issues With Sub Zero 632 Freezer
You might encounter several common issues with the Sub Zero 632 freezer that impact its performance. Understanding these problems can help you effectively troubleshoot and maintain your appliance.
Temperature Problems
Temperature fluctuations often arise when the freezer doesn’t maintain the desired freezing temperatures. Possible causes include:





- Damaged Door Seals: Inspect door seals for cracks or gaps that allow warm air in. Replace damaged seals for optimal performance.
- Blocked Vents: Check the air vents inside the freezer. Remove any obstructions to ensure proper airflow.
- Dirty Condenser Coils: Clean the condenser coils regularly. Dirty coils hinder efficiency, causing the freezer to work harder and struggle with temperature regulation.
- Improper Temperature Settings: Ensure the temperature settings are correctly adjusted. Ideally, the freezer temperature should be set between -5°F and 0°F.
Noise Issues
Unusual noises can indicate problems with your freezer. Noise issues may be caused by:
- Vibration Sounds: Ensure the freezer is level. Adjust the feet if necessary to minimize vibrations.
- Fan Noises: Listen for sounds from the evaporator fan. A faulty fan might need replacement for effective cooling.
- Compressor Sounds: Occasionally, compressors experience louder cycling. If the noise is excessive or abnormal, consult a professional for evaluation.
By addressing these common issues promptly, you can improve the performance of your Sub Zero 632 freezer and extend its lifespan.
Troubleshooting Steps
Follow these steps to diagnose and fix your Sub Zero 632 freezer issues effectively. These insights help pinpoint the problem and restore functionality.
Checking Power Supply
Ensure your freezer receives power. Check the following:
- Power Cord: Inspect for damage or loose connections.
- Outlet: Plug another device into the outlet to confirm it works.
- Circuit Breaker: Look for tripped breakers and reset if necessary.
Addressing any power issues is crucial for operational functionality.





Inspecting Door Seals
Examine the door seals for integrity. They play a significant role in maintaining temperature. Consider these actions:
- Visual Inspection: Look for cracks, tears, or deformities in the seals.
- Tissue Test: Close the door on a piece of tissue. If it slips out easily, seals require replacement.
- Clean Seals: Use soap and water to remove debris that may affect the seal’s effectiveness.
Ensuring proper sealing keeps cold air inside and prevents warm air from entering.
Evaluating Control Settings
Accurate control settings directly impact freezing performance. Check the following:
- Temperature Settings: Ensure the freezer’s temperature is set to at least 0°F (-18°C).
- Thermostat Function: Test the thermostat for responsiveness. Adjust settings back and forth to feel for proper operation.
- Mode Setting: Confirm the freezer is in the correct mode for intended usage.
Reviewing these settings helps optimize the freezer’s ability to maintain temperatures efficiently.
When To Seek Professional Help
Consider calling a technician when you’ve tried basic troubleshooting but your Sub Zero 632 freezer still isn’t working. Signs that indicate professional assistance is necessary include:
- Persistent Temperature Issues: If the freezer consistently fails to maintain the recommended temperature of 0°F (-18°C), a deeper issue could exist that requires expert evaluation.
- Frequent Noises: If you hear unusual sounds such as loud humming, clicking, or grinding that don’t dissipate after a short time, it signals a possible mechanical failure.
- Visible Damage: If you notice signs of physical damage to the appliance, such as dents, warping, or torn door seals, it’s crucial to consult a professional to avoid further complications.
- Electrical Problems: If the freezer trips circuit breakers or experiences power fluctuations, an expert should inspect the electrical components to ensure safety.
- Frost Buildup: If there’s excessive frost or ice accumulation inside the freezer, that could indicate issues with airflow or defrosting mechanisms, which typically require specialized knowledge to address.
- Refrigerant Leaks: If you detect a refrigerant smell or notice oily residue around the unit, it’s best to seek help immediately, as refrigerant poses health risks.
- Age of the Appliance: If your freezer is over ten years old and frequently develops problems, consulting a technician for a comprehensive check may prevent costly repairs down the line.
By keeping an eye out for these signs and contacting a professional when needed, you ensure the longevity and efficiency of your Sub Zero 632 freezer.
Conclusion
Dealing with a Sub Zero 632 freezer that’s not working can be frustrating but don’t lose hope. By following the troubleshooting steps outlined, you can often identify and resolve the issue without needing a technician.
Remember to keep an eye on those door seals and clean those condenser coils regularly. If problems persist or if you notice any signs of more serious issues, reaching out to a professional can save you time and hassle.
With a little attention and care, your freezer can get back to doing what it does best—keeping your food fresh and your kitchen running smoothly.
Frequently Asked Questions
What are common issues with the Sub Zero 632 freezer not freezing properly?
Common issues include damaged door seals, blocked air vents, dirty condenser coils, and incorrect temperature settings. These factors can prevent the freezer from maintaining the desired temperature and lead to food spoilage.
How can I troubleshoot my Sub Zero 632 freezer?
Start by checking the power supply, inspecting door seals, clearing air vents, and cleaning the condenser coils. Also, adjust the temperature settings to at least 0°F (-18°C) and listen for any unusual noises that could indicate a problem.
When should I seek professional help for my Sub Zero 632 freezer?
Contact a technician if you notice persistent temperature issues, unusual noises, visible damage, electrical problems, excessive frost buildup, or refrigerant leaks. Persistent problems can indicate underlying issues that require expert attention.
How do I check the door seals on my freezer?
Inspect the door seals visually for cracks or gaps. Perform a tissue test by closing the door on a piece of paper; if it pulls out easily, the seal might be compromised. Clean the seals to improve efficiency.
What temperature should my Sub Zero 632 freezer be set to?
The ideal temperature for the Sub Zero 632 freezer is at least 0°F (-18°C). Keeping it at this temperature ensures optimal food preservation and prevents spoilage.
What advanced features does the Sub Zero 632 freezer have?
The Sub Zero 632 freezer boasts a dual refrigeration system, precise temperature control, and innovative airflow design. These features work together to enhance food preservation and maintain consistent freezing temperatures.
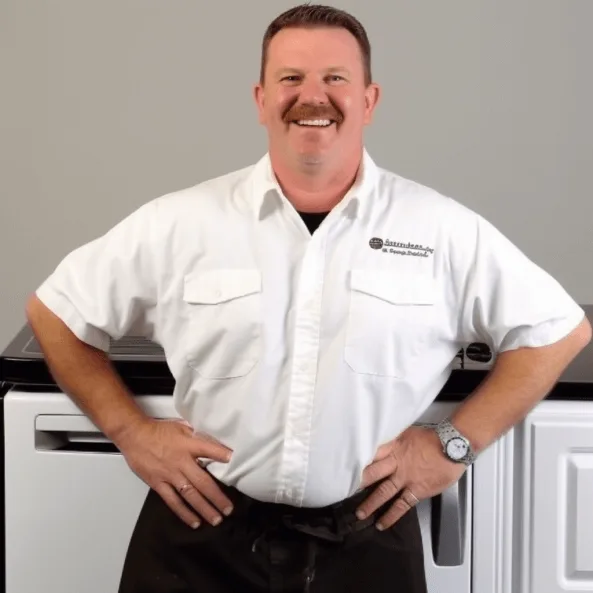
Hey, I’m Jake. I focus on cooling systems at Appliance Mastery, like fridges, freezers, and air conditioners.
I’ve worked in appliance repair for more than ten years and I’m certified through NASTeC. I’ve seen just about every fridge issue you can imagine.
My goal is to help you fix problems without stress. Whether it’s a freezer that won’t cool or an AC that keeps beeping, I’m here to walk you through it.