Is your ice maker refusing to produce those refreshing cubes on demand? You’re not alone. Many people face this frustrating issue, especially during hot summer days when a cold drink is a must.
Key Takeaways
- Identify Common Issues: Understand typical problems with ice makers, such as clogged water lines, faulty inlet valves, and broken trays, to effectively troubleshoot.
- Power and Water Supply Checks: Ensure the ice maker is powered and that the water supply is clear and unobstructed before proceeding with further troubleshooting.
- Regular Maintenance: Clean your ice maker regularly using vinegar and water to prevent mineral buildup and maintain optimal functioning.
- Optimal Freezer Temperature: Maintain your freezer’s temperature between 0°F and 5°F for efficient ice production, and check this periodically.
- Inspect Frequently: Conduct routine inspections of the ice maker’s components to catch potential issues early and avoid major malfunctions.
- Know When to Seek Help: Recognize signs that indicate the need for professional service, such as persistent ice production issues, unusual noises, water leaks, or temperature fluctuations.
Common Issues With Freezer Ice Makers
Ice makers can encounter a variety of issues that prevent them from working effectively. Understanding these common problems can help you troubleshoot the situation.
Clogged Water Line
A clogged water line restricts the flow of water to the ice maker. This can happen due to mineral buildup or debris. To resolve this, inspect the water line regularly. You can flush the line by disconnecting it and using a vinegar-water solution. Also, check for kinks in the line that may block water flow.
Faulty Water Inlet Valve
A faulty water inlet valve prevents water from entering the ice maker. If you notice no water filling the ice tray, test the valve for continuity using a multimeter. If it doesn’t pass the test, replace the valve. Ensure the water supply is turned on and there are no blockages.
Broken Ice Cube Tray
A broken ice cube tray can lead to incomplete or no ice production. If the tray is cracked or damaged, consider replacing it. Check that the tray is aligned properly and not obstructed by any components. Review the user manual for specific replacement instructions tailored to your model.
Addressing these common issues can help restore the functionality of your freezer ice maker, ensuring that you enjoy refreshing ice for your beverages year-round.
Troubleshooting Steps
When your freezer ice maker stops working, follow these troubleshooting steps to identify and resolve the issue.
Check Power Supply
Ensure your ice maker has power. Check that it’s plugged in and the outlet is functional. You can do this by plugging another device into the same outlet. If the outlet is dead, investigate your home’s circuit breaker for tripped circuits. Reset any breakers as needed and try the ice maker again.
Inspect the Water Supply
Confirm that the water supply is unobstructed. Check for kinks or bends in the water line. Look for any mineral buildup that might clog the line. If necessary, disconnect the water line and clean it using warm water and mild soap. After cleaning, reconnect the line and ensure it’s tightly sealed.
Clean the Ice Maker
Regular cleaning keeps your ice maker functioning perfectly. Unplug the ice maker and remove any leftover ice. Use a mixture of one part vinegar and one part water to clean the inside surfaces. Wipe down the ice bin and any removable parts. Rinse with clean water and dry thoroughly before plugging the unit back in. This cleaning process prevents mineral and mold buildup, which can affect ice production.
Maintenance Tips
Maintaining your freezer’s ice maker ensures it runs smoothly and produces ice efficiently. Follow these tips for optimal performance.
Regular Cleaning
Clean your ice maker regularly to prevent mineral buildup and maintain proper operation. Use a mixture of vinegar and water to wipe down the interior surfaces and components. Focus on areas like the ice bin and water reservoir. Clean once every few months or whenever you notice any ice discoloration or odor. Additionally, remove ice from the bin regularly to ensure fresh ice production.
Proper Temperature Settings
Set your freezer’s temperature between 0°F and 5°F for optimal ice production. If the temperature is too high, the ice maker may not function correctly. Use a thermometer to confirm the temperature, especially if your freezer lacks a built-in display. Adjust the settings as needed and allow 24 hours for changes to take effect.
Routine Inspections
Inspect your ice maker routinely to catch potential issues early. Check the water supply line for kinks or blockages that could disrupt flow. Examine the inlet valve for signs of wear or damage. Confirm that the ice tray is intact and sits properly in the maker. Regular inspections help ensure any problems are addressed before they escalate.
When to Call a Professional
Knowing when to seek professional help for your freezer ice maker can save time and prevent further issues. If you notice persistent problems despite troubleshooting, consider contacting an expert.
Signs of Major Malfunctions
- No ice production: If the ice maker isn’t producing any ice after checking the power and water supply, this points to a serious issue.
- Unusual noises: Strange sounds during operation, like grinding or banging, may indicate a mechanical failure.
- Water leaks: Puddles around the ice maker or freezer may signal a broken water line or faulty seal.
- Temperature fluctuations: If the freezer temperature is consistently above the ideal range of 0°F to 5°F, it can affect ice production.
- Service fees: Expect an initial diagnostic fee around $50 to $100, depending on your location.
- Parts replacement: Cost varies by part; expect $20 to $200 for items like water inlet valves or ice trays.
- Labor costs: Professional labor generally ranges from $80 to $150 per hour, adding to the overall expense.
Understanding these signs and costs helps you make informed decisions regarding professional assistance, ensuring your ice maker functions smoothly.
Conclusion
Getting your ice maker back in action doesn’t have to be a hassle. By following the troubleshooting steps and maintenance tips outlined, you can tackle common issues and enjoy fresh ice whenever you need it. Regular checks and cleaning can go a long way in preventing future problems.
If things still aren’t working after your efforts don’t hesitate to reach out to a professional. They can help diagnose any deeper issues and get your ice maker running smoothly again. With a little patience and care, you’ll be sipping cold drinks in no time.
Frequently Asked Questions
Why is my ice maker not producing ice?
The most common reasons for an ice maker not producing ice include clogged water lines, faulty water inlet valves, or broken ice cube trays. Inspecting these components can help you identify and resolve the issue.
How can I unclog my ice maker’s water line?
To unclog the water line, look for mineral buildup or debris. Regularly inspect your lines and flush them with a mixture of vinegar and water to maintain good water flow.
How do I test the water inlet valve?
You can test the water inlet valve using a multimeter. Disconnect the power and water supply, then remove the valve and check its continuity. A lack of continuity indicates that it needs replacement.
When should I replace my ice cube tray?
If you notice incomplete ice production or damage to the tray itself, it is time to replace it. A functional tray is essential for proper ice formation.
How often should I clean my ice maker?
Clean your ice maker every few months or whenever you see discoloration or detect odd odors. Regular cleaning helps prevent mineral buildup and ensures optimal performance.
What temperature should my freezer be set at for optimal ice production?
For the best ice production, set your freezer temperature between 0°F and 5°F. This temperature range allows your ice maker to function efficiently.
What are signs that I need to call a professional for ice maker issues?
Call a professional if you experience no ice production, unusual noises, water leaks, or temperature fluctuations. Persistent problems may require expert diagnosis and repair.
What costs should I expect when calling for ice maker repair?
Potential costs include diagnostic fees, parts replacement, and labor charges. It’s wise to get a quote upfront to understand the total expenses before proceeding with repairs.
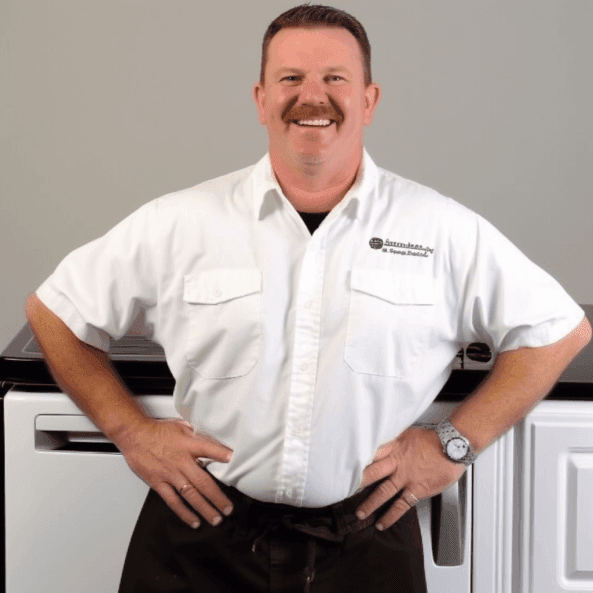
Jake Newman is Appliance Mastery’s expert on refrigeration and cooling systems. With over a decade of experience in the appliance repair industry and certification from NASTeC, Jake is a trusted source of knowledge for homeowners who want to troubleshoot and repair their fridges, freezers, and air conditioning units.